High Pressure Laminate (HPL) - CNC Milling Guide
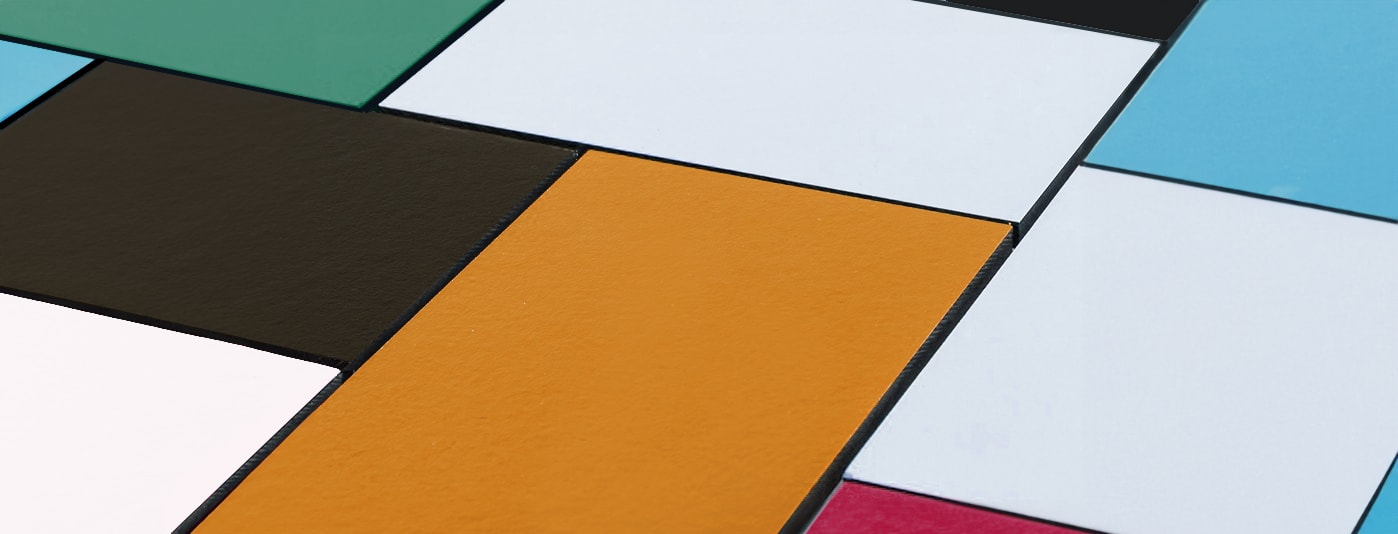
Introduction
High-Pressure Laminate is a type of surfacing material composed of layers of kraft paper impregnated with resin and bonded under high heat and pressure. The top layer is typically a decorative paper with a printed pattern or color, and the final product is known for its durability, resistance to wear, and versatility.
HPL is commonly used for countertops, furniture surfaces, wall panels, and other decorative applications.
Milling HPL on Evo CNC
Milling compact laminate on EVO is possible but requires a few precautions. We recommend to use solid carbide or diamond bits, and start at a low tool engagement and depth of cut to obtain a decent surface finish. Because the material is very dense, so vibration can easily appear.
In general EVO will cut it just fine, but might not be suited for a business scale production and finishing, like a PRO or FAB.
As always: start with our safe parameters and increase them progressively to find the sweet spot for your own setup.
- Machine : Mekanika EVO S / High-Z / AMB 1050W
- End mill : Ø 6mm / 2 Flutes Carbide / Upcut spiral bit
- Feed rate : 2200 mm/min
Spindle speed : 18 000 rpm - Depth of cut : 2 mm
Milling HPL on Pro or Fab CNC Machines
Milling compact laminate on PRO & FAB works perfectly well. The main challenge will be to find parameters optimizing tool lifetime as the material can be pretty aggressive on tools. Chips should not be burnt or melted, a good indicator is their color : chips color should not be different than the panel. In general, passes should be shallower and chip load lower than most materials due to the density of HPL. But there is a wide range of variations depending on fixture, tool used, etc.
So as always, we recommend to start with the recommended safe parameters and increase them progressively to find the sweet spot for your own setup.
Recommended parameters:
- Machine : Mekanika PRO S / Standard-Z / VFD 2.2kW
- End mill : Ø 6mm / 2 Flutes Carbide / Upcut spiral bit
- Feed rate : 2 800 mm/min
- Spindle speed : 19 000 rpm
- Depth of cut : 3 mm
Tips & Tricks
- Using tools that dissipate heat easily is mandatory (solid carbid or diamon bits)
- Use ramps or helix instead of plunges to increase your tool's lifetime.
- Chips should not be burnt/melted (too fast spindle speed) nor look like teared out chunks of material (too fast feed). Chips changing colors is a good indicator of heat building.
- If the surface finish is not good, it can be related to various things:
- check that your stock is fixed strong enough and not vibrating
- check your tool's edges to see if it is damaged
- use the shortest tool possible for the job to avoid tool deflection
- Test different feeds/speeds (most likely : reduce feed rate or increase spindle speed, within the machine's capabilities and while maintaining an acceptable chip load).
Feed & Speed Calculator
You can find here a link to a feed and speed calculator for the most classic materials, and safe values adapted to each of our machines.
MEKANIKA CNC FEED & SPEED CALCULATOR
IMPORTANT NOTE: this is made to help you find parameters for your milling, but you should always think by yourself and enter cutting parameters that are matching your own setup.
Calculating the theorical values in this table is easy, but many parameters in your setup may make them unfit for your case. Always start with low engagement and speed, and test deeper/quicker parameters progressively.
About Mekanika
Mekanika is a Belgian company based in Brussels whose ambition is to make local production more accessible thanks to a 100% open-source approach.
We design and produce high quality machines for CNC milling and screen printing, which have been recognized for their reliability and ease of use. Our tools are delivered as kits and fully documented, allowing to easily adapt them to specific needs.
Visit our shop to find out more, or check out our online resources and tutorials to continue learning.