PMMA (Acrylic) - CNC Milling Guide
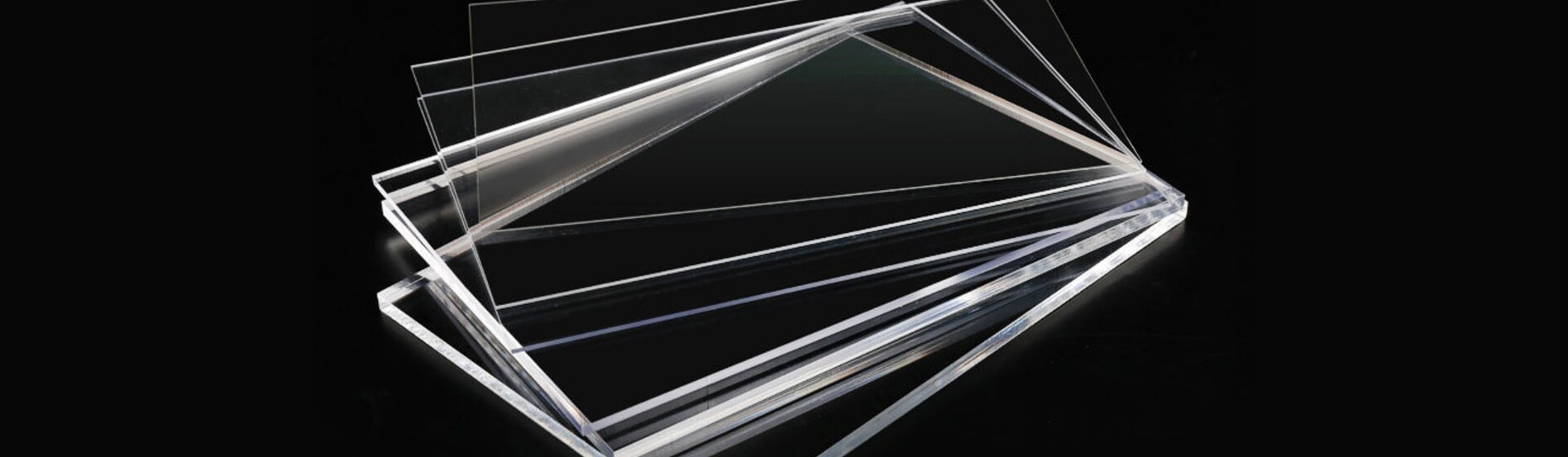
Introduction
PMMA stands for Polymethyl Methacrylate, which is commonly known as acrylic or Plexiglas. It is a transparent thermoplastic with properties that make it suitable for a variety of applications.
PMMA is a good material for milling purposes, especially when transparency and ease of machining are important considerations.
Milling PMMA on Evo CNC
EVO can cut nicely in PMMA but you'll have to be very careful with the tools and cutting parameters as it is less forgiving than most material .
PMMA has a relatively low melting point, so care must be taken to avoid excessive heat during milling to prevent melting and deformation. Usually this is achieved by increasing feed rate, but as PMMA is quite hard, EVO shouldn't be run too fast in it.
If you get melted plastics, you can also reduce the spindle speed.
We recommend using a 1 flute bit (2 is also ok) to lower the feed rate, and use low depth of cut and/or stepover to be gentle on EVO's axis.
Using an air compressor to remove the chips during milling is also a good idea as the main concern is chips melting and clogging the tool.
Always test with safe parameters and increase them progressively to find the sweet spot for your own setup.
Parameters used in the video:
- Machine : Mekanika EVO S / High-Z / AMB 1050W
- End mill : Ø 6mm / 2 Flutes Carbide / Upcut spiral bit
- Feed rate : 2200 mm/min
- Spindle speed : 18 000 rpm
- Depth of cut : 2 mm
Milling PMMA on Pro or Fab CNC
PMMA milling is less forgiving than most material so special care has to be taken when programming your CAM. With some testing you can achieve perfect results on PRO and FAB.
PMMA has a relatively low melting point, so the main concern is to avoid excessive heat during milling. Usually this is achieved by increasing feed rate, but be carefull not to go to fast as PMMA is a hard material.
If you get melted plastics, you can also reduce the spindle speed.
We recommend using a 1 flute bit (2 can also be ok) which have better chip evacuation and to lower the feed rate.
Using an air compressor to remove the chips during milling is also a good idea to clear them and help with tool cooling.
We recommend to test "safe" parameters and increase them progressively to find the sweet spot for your own setup.
Recommended parameters:
- Machine : Mekanika PRO S / Standard-Z / VFD 2.2kW
- End mill : Ø 6mm / 2 Flutes Carbide / Upcut spiral bit
- Feed rate : 2 800 mm/min
- Spindle speed : 19 000 rpm
- Depth of cut : 3 mm
Tips & Tricks
- Use tools specialised for plastics/acrylics for better results (usually 1 flute, maximum 2 flutes for roughing), with a high upcut helix angle.
- Do not use downcut bits with plastics as it will create to much heat at the bottom of the tool and melt the material.
- A continuous blow of compressed air on the tool will help a lot with chip clearing and cooling.
- A good setting will produce relatively big chips, allowing heat dissipation.
- A good setting will not have any material stuck in the tools flute.
- We recommend using a strategy of roughing + finishing pass when precision is needed in the part.
- Use ramps or helix instead of plunge to increase your tool's lifetime.
- If the surface finish is not good, it can be related to various things:
- check that your stock is fixed strong enough and not vibrating
- check your tool's edges to see if it is damaged
- use the shortest tool possible for the job to avoid tool deflection
- Test different feeds/speeds (most likely : reduce feed rate or increase spindle speed, within the machine's capabilities and while maintaining an acceptable chip load).
Feed & Speed Calculator
You can find here a link to a feed and speed calculator for the most classic materials, and safe values adapted to each of our machines.
MEKANIKA CNC FEED & SPEED CALCULATOR
IMPORTANT NOTE: this is made to help you find parameters for your milling, but you should always think by yourself and enter cutting parameters that are matching your own setup.
Calculating the theorical values in this table is easy, but many parameters in your setup may make them unfit for your case. Always start with low engagement and speed, and test deeper/quicker parameters progressively.
About Mekanika
Mekanika is a Belgian company based in Brussels whose ambition is to make local production more accessible thanks to a 100% open-source approach.
We design and produce high quality machines for CNC milling and screen printing, which have been recognized for their reliability and ease of use. Our tools are delivered as kits and fully documented, allowing to easily adapt them to specific needs.
Visit our shop to find out more, or check out our online resources and tutorials to continue learning.