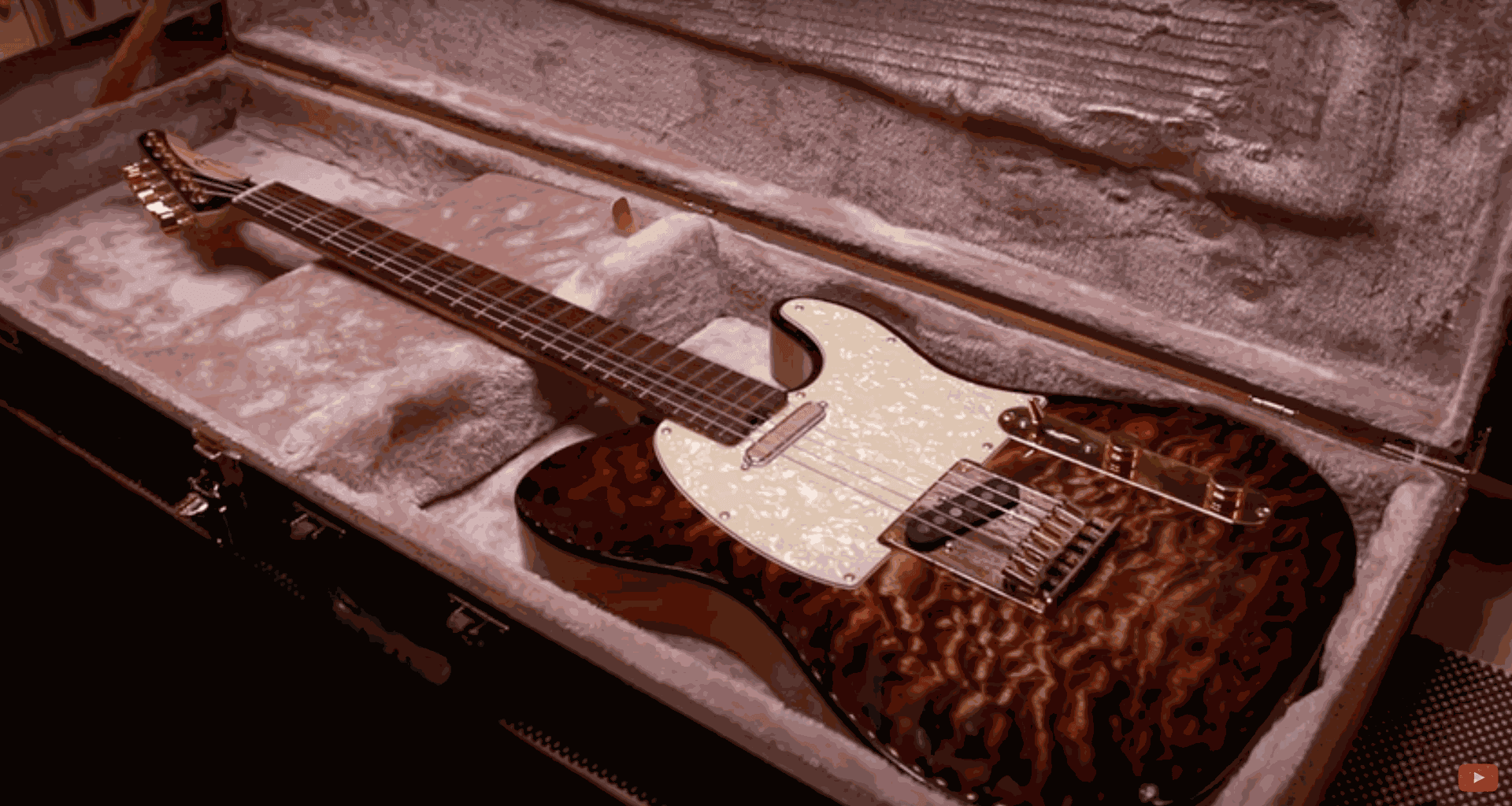
This guitar was imagined and designed by Hussein of Barada Guitars, with the help of his friend Austin, who lent his expertise to the design of the CAD files.
This project is relatively easy, but you need a good clamping setup as the stock is relatively big. We recommend using at least 1 clamp (or screw) every 10cm to reduce the vibrations and enhance the quality of your surface finish.
We suggest you tackle this one after you’ve gained some experience with CNC milling.
If you feel comfortable with Fusion360, you can modify the parameters of this project to make the bird feeder fit any plate you want. Check out our article to learn how to work with parametric designs.
The bird feeder is made out of one bigger piece of 12 mm plywood and one ceramic plate (available in any DIY store).
530 x 229 x 12 mm
We used plywood for our bird feeder, but you can use any material you want for this project. Please keep in mind that the project is made for 12 mm thick material and that the joins making everything fit into each other have to be the exact size of your stock.
If you want to use another thickness of the material, please check out our parametric design article to learn how to edit parametric files.
Oversize your stock (+20mm at each side) to be able to secure it properly to the spoiler board. Securing it firmly to your spoiler board will not only prevent your piece to fly around but will also reduce the amount of vibration during milling and by means improve the surface finish. Check our “Feeds and Speeds explained” article to learn more about the influence of parameters on your milling results.
We used a 3 mm 2-flutes flat down-cut end mill for milling our pieces.
This piece is made out of 2 operations:
We start by milling the hole for the rope with a bore operation. The spindle should run between 20 000 and 25 000 rpm as the feed rate is 1725 mm/min with 1.5 mm passes.
The second operation is a Contour2D operation that will cut all the pieces in the stock. The spindle should run between 20 000 and 25 000 rpm as the feed rate is 1725 mm/min with 1.5 mm passes.
Mekanika is a Belgian company based in Brussels whose ambition is to make local production more accessible thanks to a 100% open-source approach.
We design and produce high quality machines for CNC milling and screen printing, which have been recognized for their reliability and ease of use. Our tools are delivered as kits and fully documented, allowing to easily adapt them to specific needs.
Visit our shop to find out more, or check out our online resources and tutorials to continue learning.
This guitar was imagined and designed by Hussein of Barada Guitars, with the help of his friend Austin, who lent his expertise to the design of the CAD files.
This project will guide you through the creation of a fully functional folding ping pong table entirely made of CNC cut wood panels.
Quentin L.
Content Creation
We decided to design some acoustic panels using our own Fab CNC to both improve acoustic and embellish our meeting room.
Martin D.
Product Design