Pour amateurs et professionnels
Mekanika propose une gamme de fraiseuses numériques pour tout type d’usinage. Evo est le choix idéal pour hobbyistes, Pro est une machine robuste et puissante, et Fab s’attaque à n’importe quel matériau en forme de panneau. Choisis la machine qui te ressemble pour donner forme à tes idées.
Du hobby à la production
Evo
La meilleure machine pour démarrer
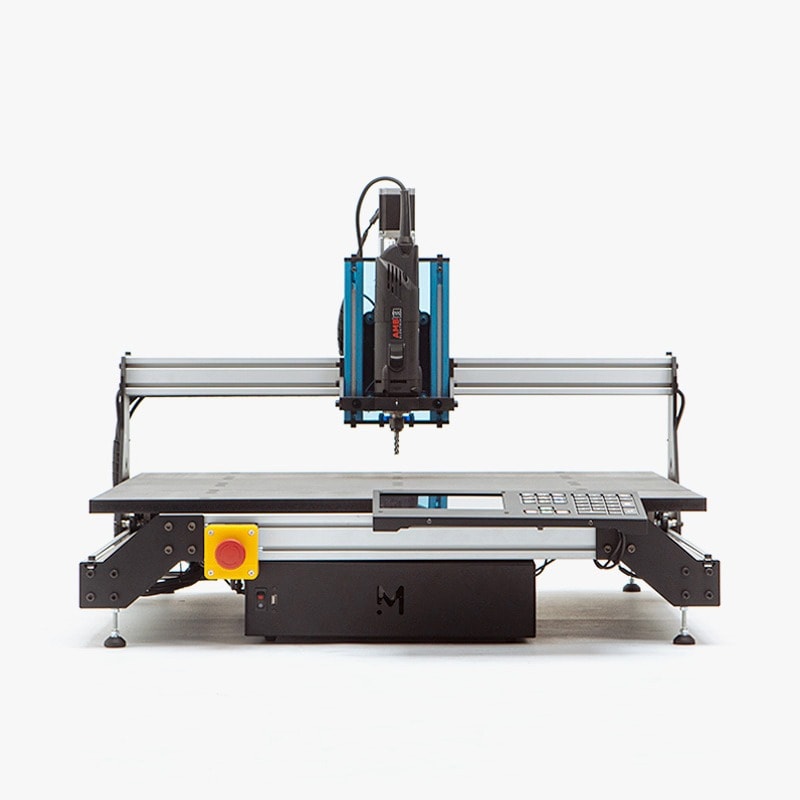
Utilisation | Hobby & semi-pro |
Fréquence | Occasionnelle |
Matériau | Plastique à bois durs |
Zone de travail | Jusqu'à 1030x1030mm |
Garantie | 5 ans |
Pro
Une machine puissante et compacte
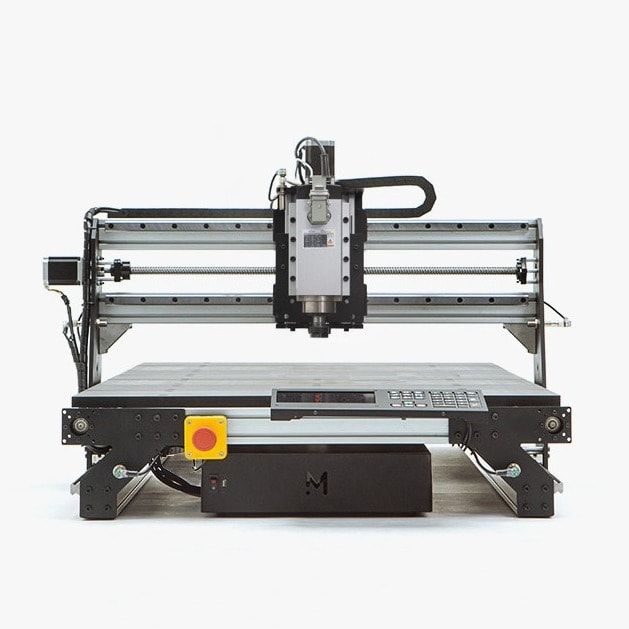
Utilisation | Semi-pro & pro |
Fréquence | Quotidienne |
Matériau | Bois durs à métaux non-ferreux |
Zone de travail | Jusqu'à 1030x1030mm |
Garantie | 5 ans |
Fab
Une fraiseuse numérique grand format
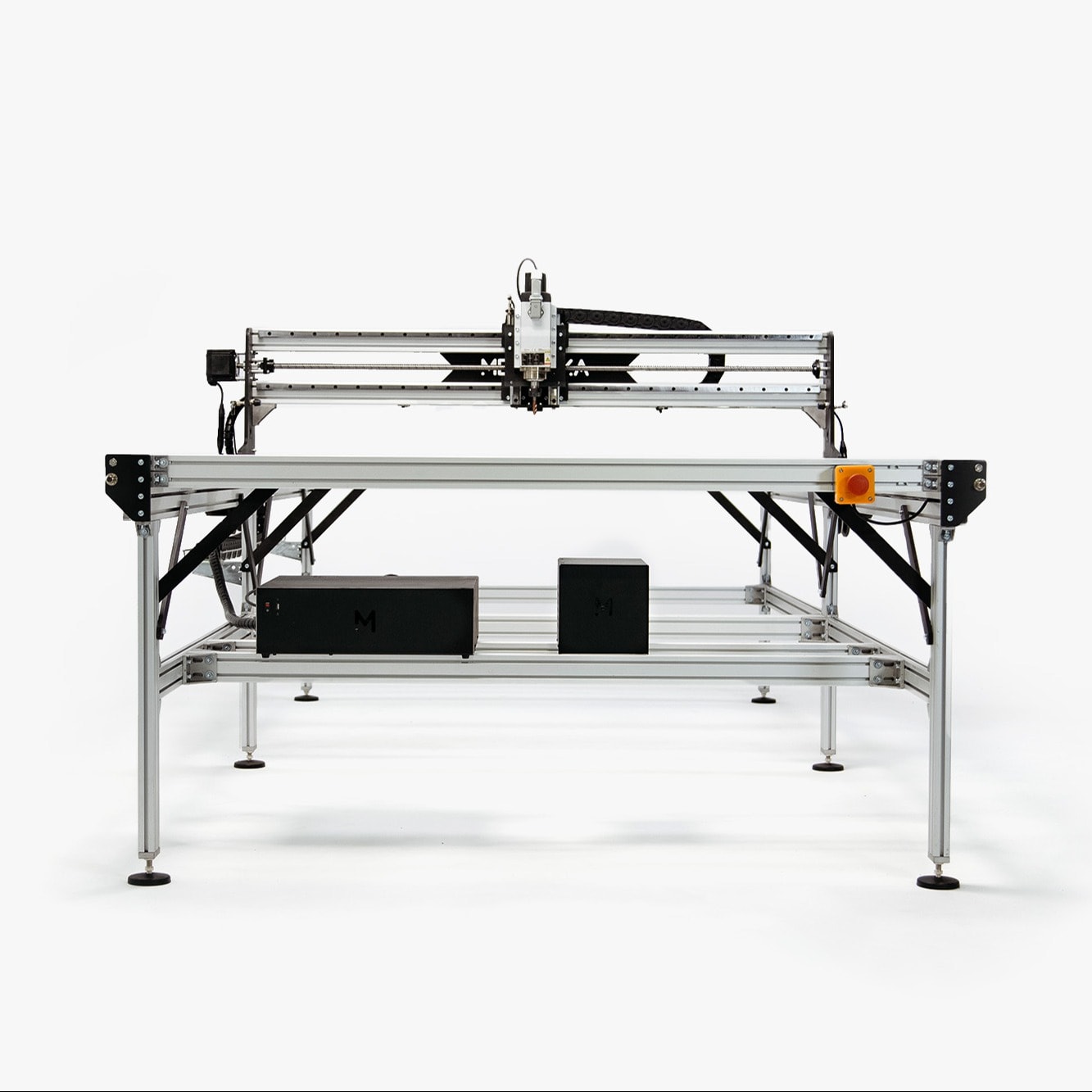
Utilisation | Pro |
Fréquence | Quotidienne |
Matériau | Bois durs à métaux non-ferreux |
Zone de travail | 1300x2700mm |
Garantie | 5 ans |
Une large gamme d' accessoires
Complète ta machine Mekanika avec notre sélection d’accessoires conçus pour maximiser sécurité, précision et confort d’usinage. Choisis la configuration idéale pour tes besoins.
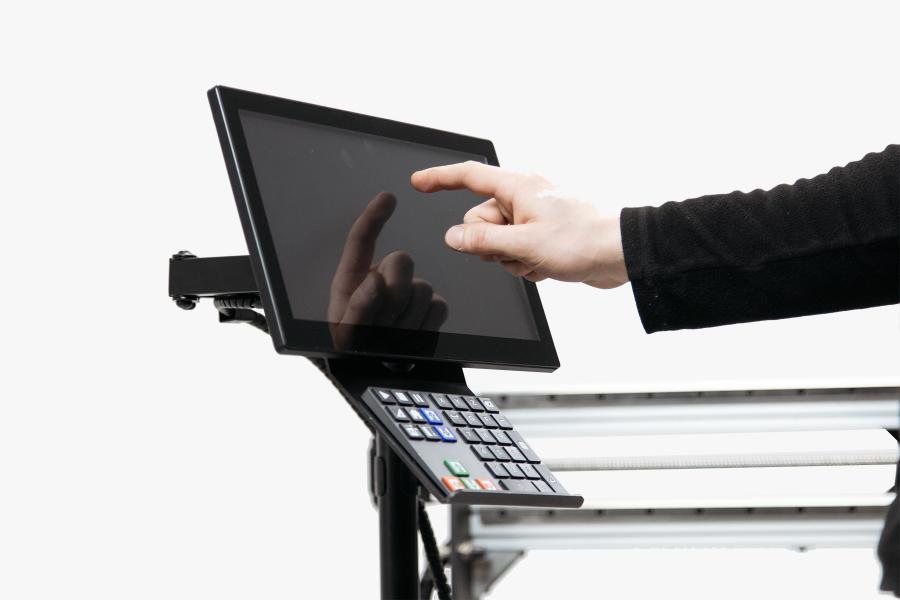
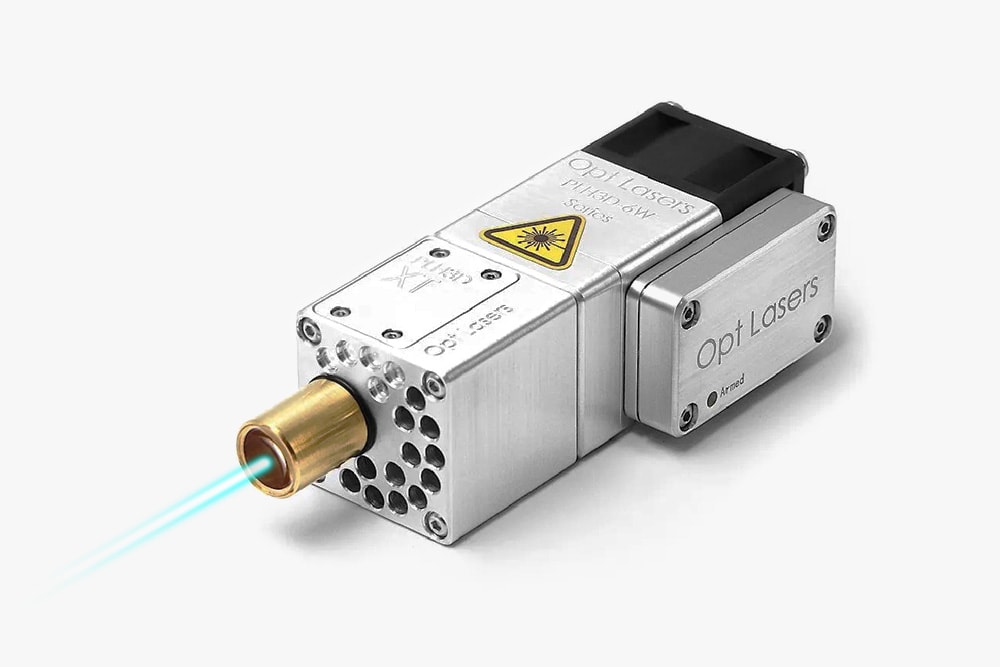
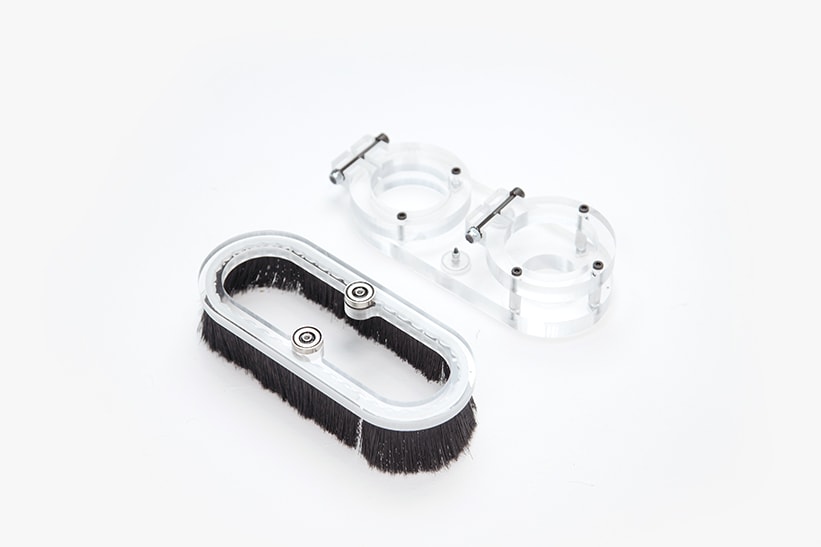
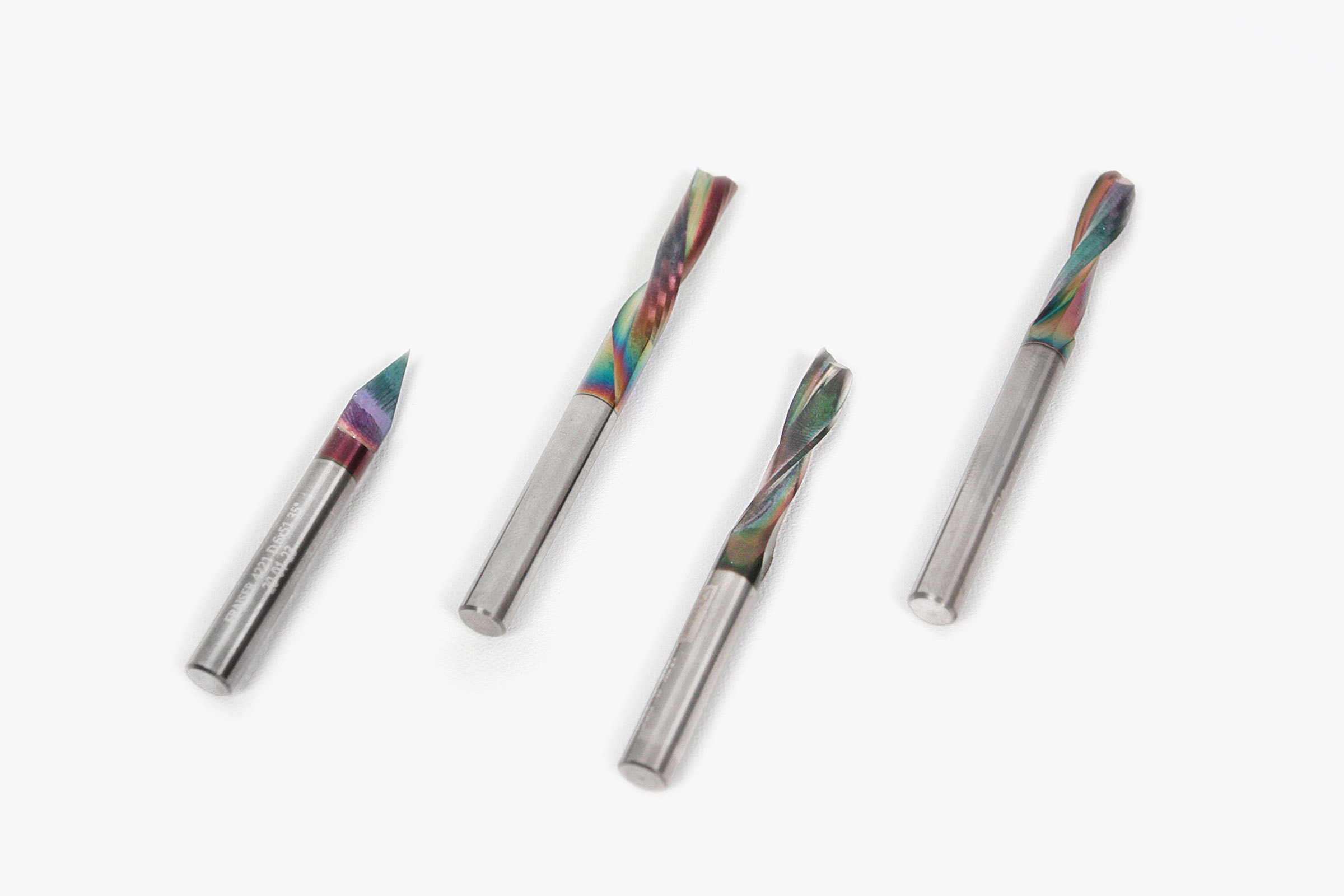
Livraison en kit
Le design des machines Mekanika est basé sur une approche ouverte et modulaire, c’est le principe open-source. Nous concevons toujours nos produits en gardant à l'esprit la modularité et le démontage : rien n'est collé ou soudé, nous utilisons des pièces standards dans la mesure du possible et tout composant peut être facilement remplacé ou réparé.
En assemblant ta machine, tu acquières de précieuses connaissances sur son fonctionnement et son entretien. Cela te permettra d’avoir une machine pour la vie.
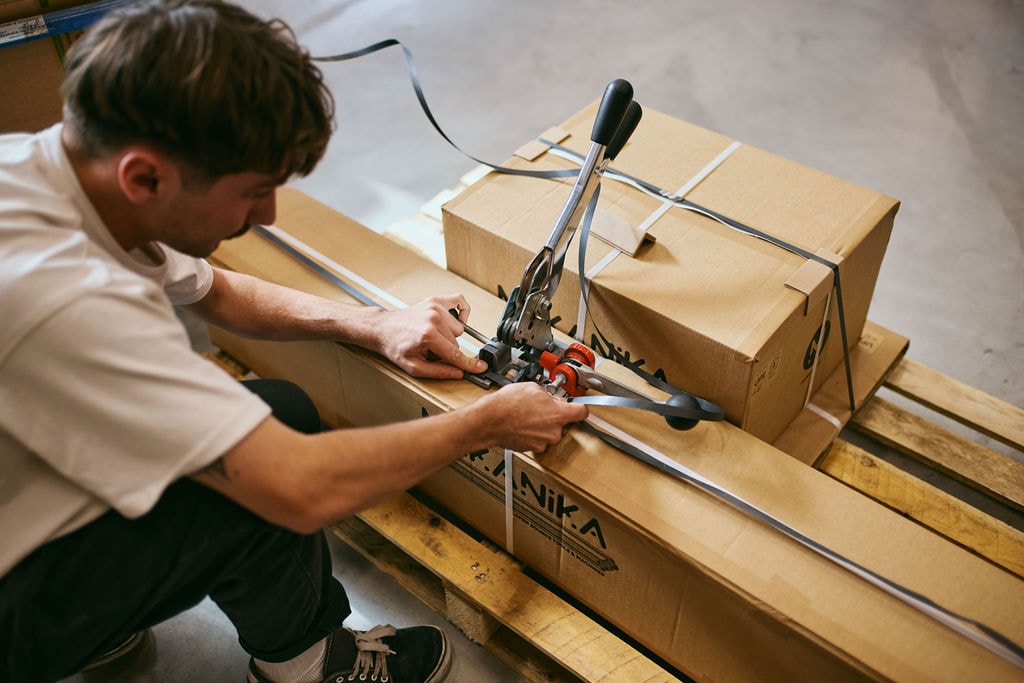
Nos ressources CNC
On construit ton aventure CNC avec toi
Laisse-toi guider pas à pas
Notre équipe a prévu des ressources pensées spécialement pour toi : une suite de tutos pour apprendre les bases du fraisage numérique de ton côté, et une série de formations pour un accompagnement plus structuré et progressif.
Le coin des makers !
Un blog inspirant et des projets CNC gratuits
Chez Mekanika, on est passionnés de fabrication numérique, et on adore partager. Dans notre blog, tu trouveras de nombreuses informations sur les techniques CNC. Et comme la meilleure façon d’apprendre, c’est en faisant, nous avons préparé des projets de fraisage CNC inspirants que tu peux télécharger immédiatement.
Plus tu comprendras ta machine, plus tu iras loin.
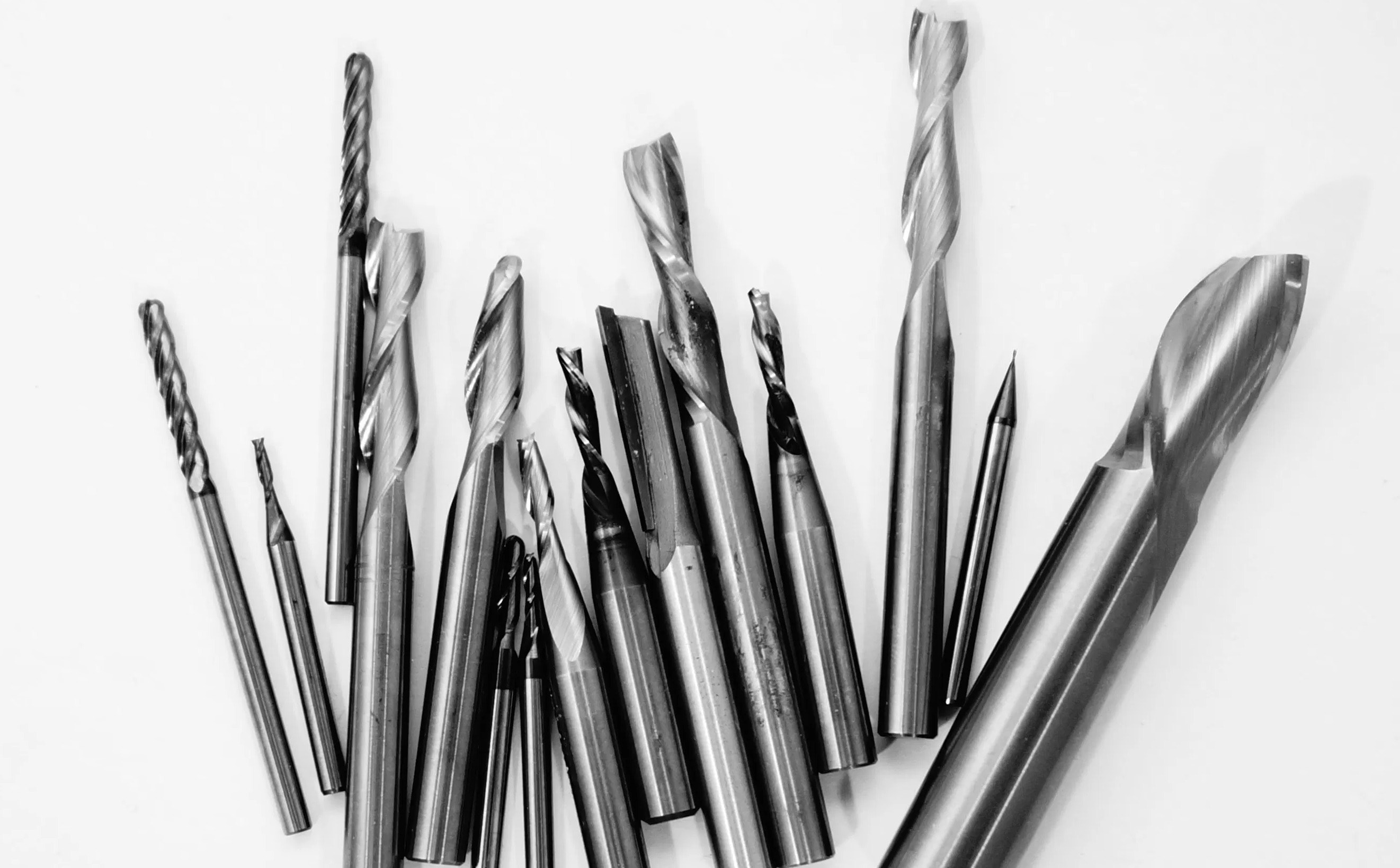
Un software intuitif
Pour faciliter la prise en main
Le logiciel Planet CNC est un logiciel complet conçu pour améliorer le fonctionnement des machines CNC. Ce logiciel est polyvalent et prend en charge un grand nombre de formats de fichiers et de fonctions afin de garantir l'efficacité et la précision des opérations CNC.
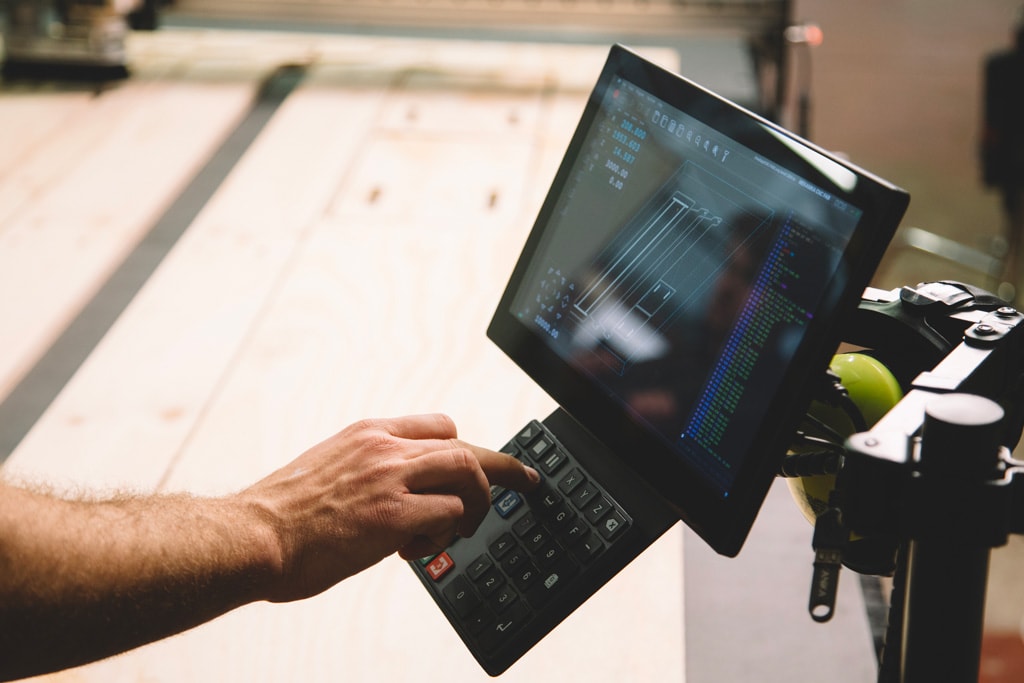
Finance ton investissement
Mekanika Financing est notre solution de financement pour professionnels, en partenariat avec Grenke. Il s'agit d'un programme de financement qui te permet d'acheter des machines Mekanika avec de faibles mensualités fixes. Le montant minimum du financement est de 500€ HTVA. Uniquement valable en France et en Belgique pour le moment.
- Le montant minimum de financement
- 500€
- Le nombre de mois maximum d'étalement
- 60
- Le temps pour analyser votre demande
- 48h