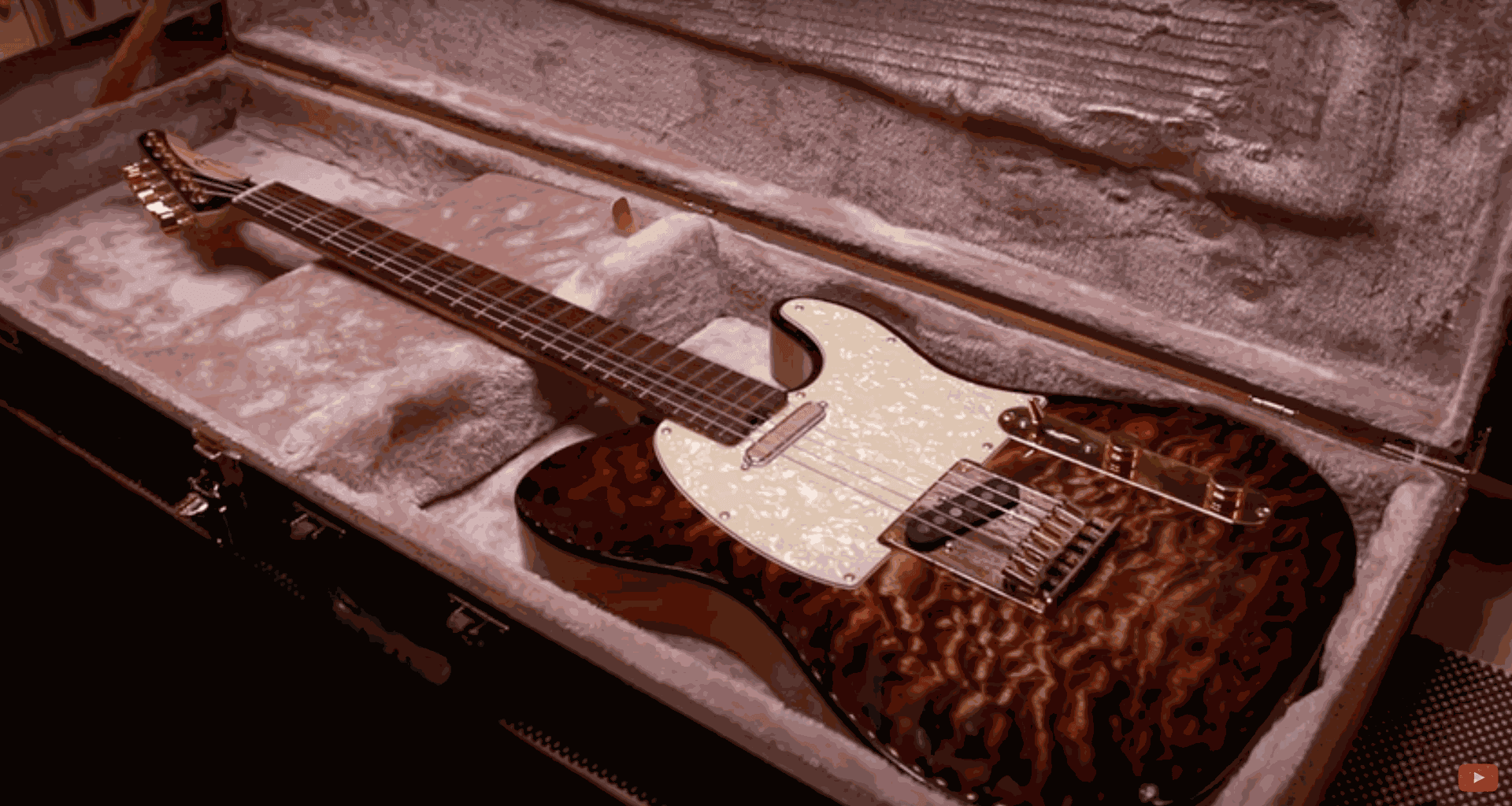
Diese Gitarre wurde von Hussein von Barada Guitars erdacht und entworfen, mit Hilfe seines Freundes Austin, der sein Fachwissen bei der Gestaltung der CAD-Dateien zur Verfügung stellte.
Dieses Projekt eignet sich hervorragend, um neue Möglichkeiten zu erforschen, indem Sie Ihre CNC-Maschine in ihrer maximalen 3D-Kapazität nutzen. Es ist das perfekte Beispiel dafür, dass eine CNC-Maschine viel präziser ist als die menschliche Hand, aber auch schneller als ein 3D-Drucker. Der Vorteil ist, dass Sie dieses Projekt aus jedem Material herstellen können, bei dem ein 3D-Drucker an seine Grenzen stößt.
Da bei diesem Projekt viel Material abgetragen wird und Präzision der Schlüssel ist, ist eine gute Klemmung sehr wichtig! Um das Teil sicher zu klemmen, haben wir uns entschieden, unser Material direkt in die Spoilerplatte zu schrauben.
Wir empfehlen, mindestens 1 Klemme (oder Schraube) alle 10 cm zu verwenden, um die Vibrationen zu reduzieren und die Qualität der Oberfläche zu verbessern.
Wenn Sie kein Fan unseres Modells sind und eine andere topografische Karte fräsen möchten, schauen Sie sich diese Website an . Sie generiert STL-Dateien von der Erdoberfläche. Diese STL-Dateien können dann in Fusion360 importiert und skaliert werden, um als Modell für das Fräsen verwendet zu werden.
Wir haben für dieses Projekt massiven Nussbaum verwendet, aber Sie können jedes beliebige Material verwenden. Um unsere 3D-Karte des Comer Sees zu fräsen, benötigen Sie ein Material, das mindestens 340 x 530 x 25 mm groß ist.
Vergessen Sie nicht, das Material an jeder Seite um mindestens 20 mm zu überdrehen, damit Sie Ihr Werkstück sicher einspannen können.
Für dieses Projekt haben wir die folgenden Schaftfräser verwendet.
Weitere Informationen über die Auswahl der Schaftfräser sowie Vorschübe und Drehzahlen finden Sie auf unserer Website .
Sie können die Schnittparameter natürlich auch an Ihre verfügbaren Schaftfräser anpassen.
Achtung ! Dieses Projekt ist sehr komplex und hat eine Menge kleiner Details. Das bedeutet, dass es auch sehr viel Zeit zum Fräsen braucht. Wenn Sie unseren G-Code so verwenden, wie er ist, beträgt die gesamte Fräszeit einige Stunden. Sie können die Fräszeit reduzieren, indem Sie die Schrittweite oder die Durchgangshöhe erhöhen, aber das führt unweigerlich zu einem Verlust an Präzision.
Um eine schöne Oberfläche zu erhalten und gleichzeitig die für die Herstellung unseres Werkstücks benötigte Zeit zu begrenzen, haben wir einen G-Code erstellt, der aus 3 Operationen besteht.
Mit einem 8-mm-Schaftfräser wird die Form des Geländes, das wir fräsen wollen, grob skizziert. Mit einem axialen und radialen Aufmaß von 1 mm stellen wir sicher, dass unsere nächsten Schaftfräser "etwas zum Anbeißen" haben. Dadurch wird nicht nur ein Verrutschen verhindert, sondern auch sichergestellt, dass unser 8-mm-Schaftfräser nicht die Präzision des fertigen Werkstücks beeinträchtigt, indem er in Material schneidet, in das er nicht schneiden sollte.
Die Spindel muss auf eine Drehzahl von 20 000 bis 25 000 U/min eingestellt werden, der Vorschub beträgt 3200 mm/min. Die Durchlaufhöhe beträgt 2,5 mm.
Um die Materialmenge zu reduzieren, die der dünne Kugelfräser abtragen muss, haben wir einen ersten Aushöhlungsvorgang mit dem 8-mm-Flachfräser hinzugefügt. Dieser Schritt entfernt den "Reisfeld"-Effekt, der nach dem ersten Arbeitsgang zurückgeblieben ist, und Sie werden sehen, wie das Terrain herausspringt. Wir behalten 0,5 mm axiales und radiales Material, damit der Kugelfräser etwas zu beißen hat.
Dieser Schritt ist nicht zwingend erforderlich, verringert aber den Verschleiß des Kugelfräsers erheblich und ermöglicht es Ihnen, den Vorschub beim nächsten Arbeitsgang zu erhöhen (was die Gesamtfräszeit verkürzt).
Die Spindel muss auf eine Drehzahl von 20 000 bis 25 000 U/min eingestellt werden, da der Vorschub 3200 mm/min beträgt. Die Schrittweite ist auf 3,5 mm eingestellt.
Dieser Schritt verleiht dem fertigen Stück seine ganze Textur und lässt jedes Detail des Geländes hervorstechen.
Durch die "Scallop"-Operation fährt der Kugelfräser in jedes Tal, auf jeden Hügel und jeden Grat unserer Karte und hinterlässt nur sehr wenige Frässpuren.
Die Spindel muss auf 20 000 bis 25 000 U/min eingestellt werden, da die Vorschubgeschwindigkeit 3500 mm/min beträgt. Die Schrittweite wird auf 0,4 mm eingestellt, um die Anzahl der Frässpuren zu reduzieren.
Mekanika ist ein belgisches Unternehmen mit Sitz in Brüssel, dessen Ambition es ist, die lokale Produktion dank eines zu 100 % Open-Source-Ansatzes zugänglicher zu machen.
Wir entwerfen und produzieren hochwertige Maschinen für CNC-Fräsen und Siebdruck, die für ihre Zuverlässigkeit und Benutzerfreundlichkeit bekannt sind. Unsere Werkzeuge werden in Kits geliefert und sind vollständig dokumentiert, sodass sie leicht an spezifische Bedürfnisse angepasst werden können.
Besuchen Sie unseren Shop um mehr zu erfahren, oder sehen Sie sich unsere Online-Ressourcen und Tutorials an, um weiter zu lernen.
Diese Gitarre wurde von Hussein von Barada Guitars erdacht und entworfen, mit Hilfe seines Freundes Austin, der sein Fachwissen bei der Gestaltung der CAD-Dateien zur Verfügung stellte.
Dieses Projekt führt Sie durch die Herstellung eines voll funktionsfähigen Klapp-Tischtennistischs, der vollständig aus CNC-geschnittenen Holzplatten besteht.
Quentin L.
Content Creation
Wir haben uns entschlossen, mit unserer eigenen Fab CNC einige Akustikplatten zu entwerfen, um sowohl die Akustik zu verbessern als auch unseren Besprechungsraum zu verschönern.
Martin D.
Product Design