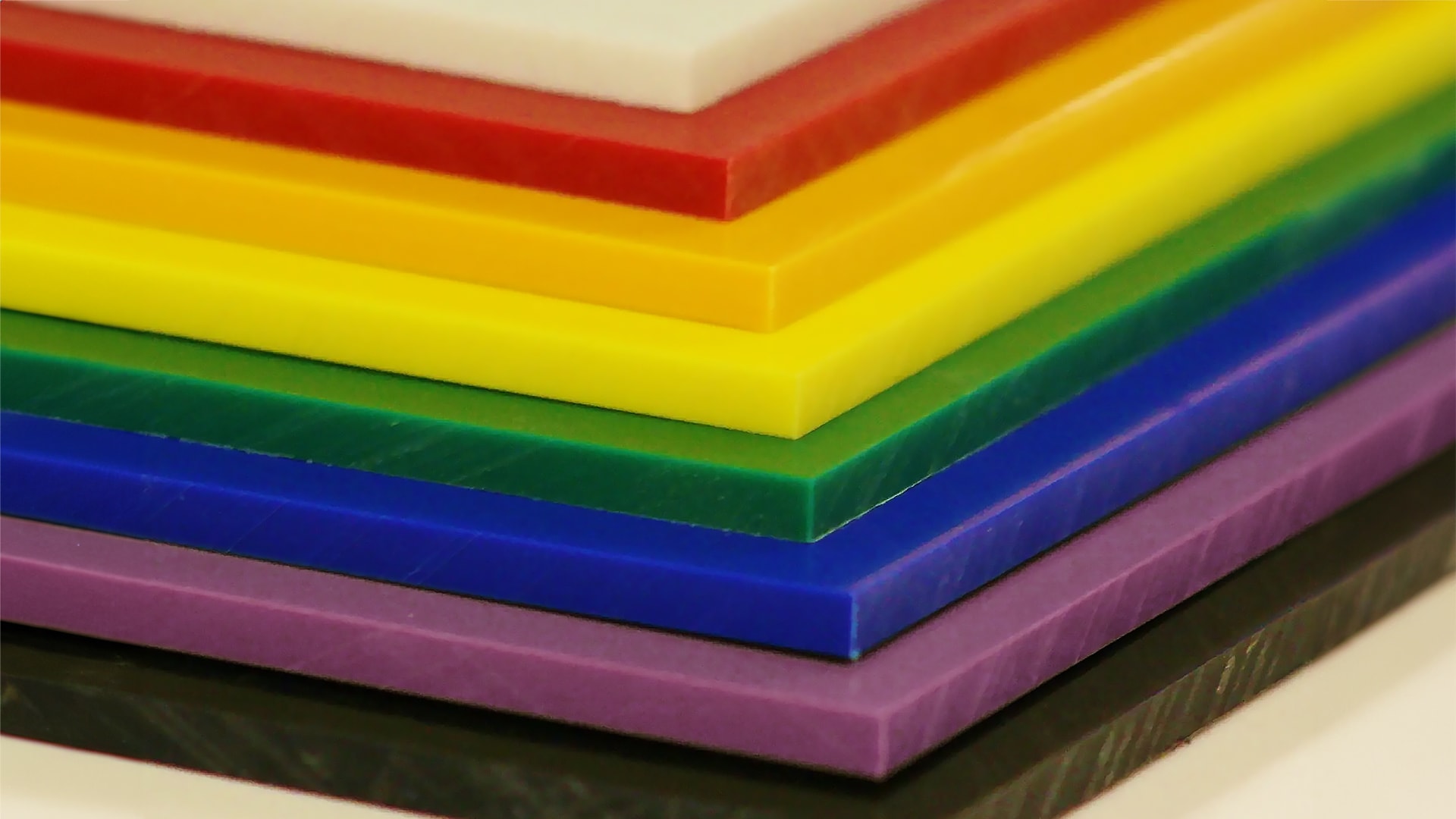
Feed rate, Spindle speed, depth of cut, type of cutter: discover all the tips you need to effectively mill HDPE using your CNC machine.
Quentin L.
Content Creation
IMPORTANT DISCLAIMER :
There is a wide range of different aluminium alloy types. Each of them have very different properties that can modify a lot their milling outcome.
Here we will be talking about the most commonly milled aluminiums (6061, 7075, 7005...) and generalize the way to mill them, but for more advanced milling parameters, please refer to metal and/or end mill suppliers for recommended feeds and speeds, and adapt them to your machine's capabilities.
EVO being an entry level CNC, it can handle some aluminium milling but it should remain occasional as it will be a bit intense for the machine.
If you take very shallow passes (but therefore extend a lot the milling time) you can still obtain perfectly nice results.
Remember that you'll most likely need to help the tool to cool down (unless the job is very short) and/or blow air to evacuate the chips : both of those actions in order to prevent the metal to melt and clog the tool, which will lead to tool breakage, the most common mistake happening when learning to mill metals.
Keep an eye on your tool, if you see any buildup of materials in it you can pause or stop the job to save your tool before it breaks. And correct your parameters to build less heat. (can be reducing the spindle rotation if it is not to low, or moving a bit faster if possible, or reducing the depth of cut, or adding coolant...).
The FAB and PRO increased rigidity and spindle power will make milling aluminium a lot easier. They'll allow faster feed rates and bigger depth of cut compared to EVO, but tool cooling will remain the main bottleneck to the parameters.
For occasional aluminium cuts, you can use simple tips like WD40 spraying to lubricate the cut and/or air blowing on the tool to evacuate chips and help cooling down the tool. But if you plan on milling longer series of aluminium jobs, then installing a fixed lubrication or air blowing system on the machine could be mandatory to free you from spraying manually the tool all along.
Always test your parameters first, keep an eye on the tool for any clogging. If materials starts to build up in the flutes and creates long strings of aluminium, it means it is to hot and aluminium chips melt and weld themselves together, which will lead to tool breaking as soon as it will be full of material.
If this happens, stop the job and change your parameters to build less heat.
(can be reducing the spindle rotation if it is not to low, or moving a bit faster if possible, or reducing the depth of cut, or adding coolant...).
You can find here a link to a feed and speed calculator for the most classic materials, and safe values adapted to each of our machines.
MEKANIKA CNC FEED & SPEED CALCULATOR
IMPORTANT NOTE: this is made to help you find parameters for your milling, but you should always think by yourself and enter cutting parameters that are matching your own setup.
Calculating the theorical values in this table is easy, but many parameters in your setup may make them unfit for your case. Always start with low engagement and speed, and test deeper/quicker parameters progressively.
Mekanika is a Belgian company based in Brussels whose ambition is to make local production more accessible thanks to a 100% open-source approach.
We design and produce high quality machines for CNC milling and screen printing, which have been recognized for their reliability and ease of use. Our tools are delivered as kits and fully documented, allowing to easily adapt them to specific needs.
Visit our shop to find out more, or check out our online resources and tutorials to continue learning.
Feed rate, Spindle speed, depth of cut, type of cutter: discover all the tips you need to effectively mill HDPE using your CNC machine.
Quentin L.
Content Creation
Feed rate, Spindle speed, depth of cut, type of cutter: discover all the tips you need to effectively mill cork using your CNC machine.
Quentin L.
Content Creation
Feed rate, Spindle speed, depth of cut, type of cutter: discover all the tips you need to effectively mill softwoods using your CNC machine.
Quentin L.
Content Creation