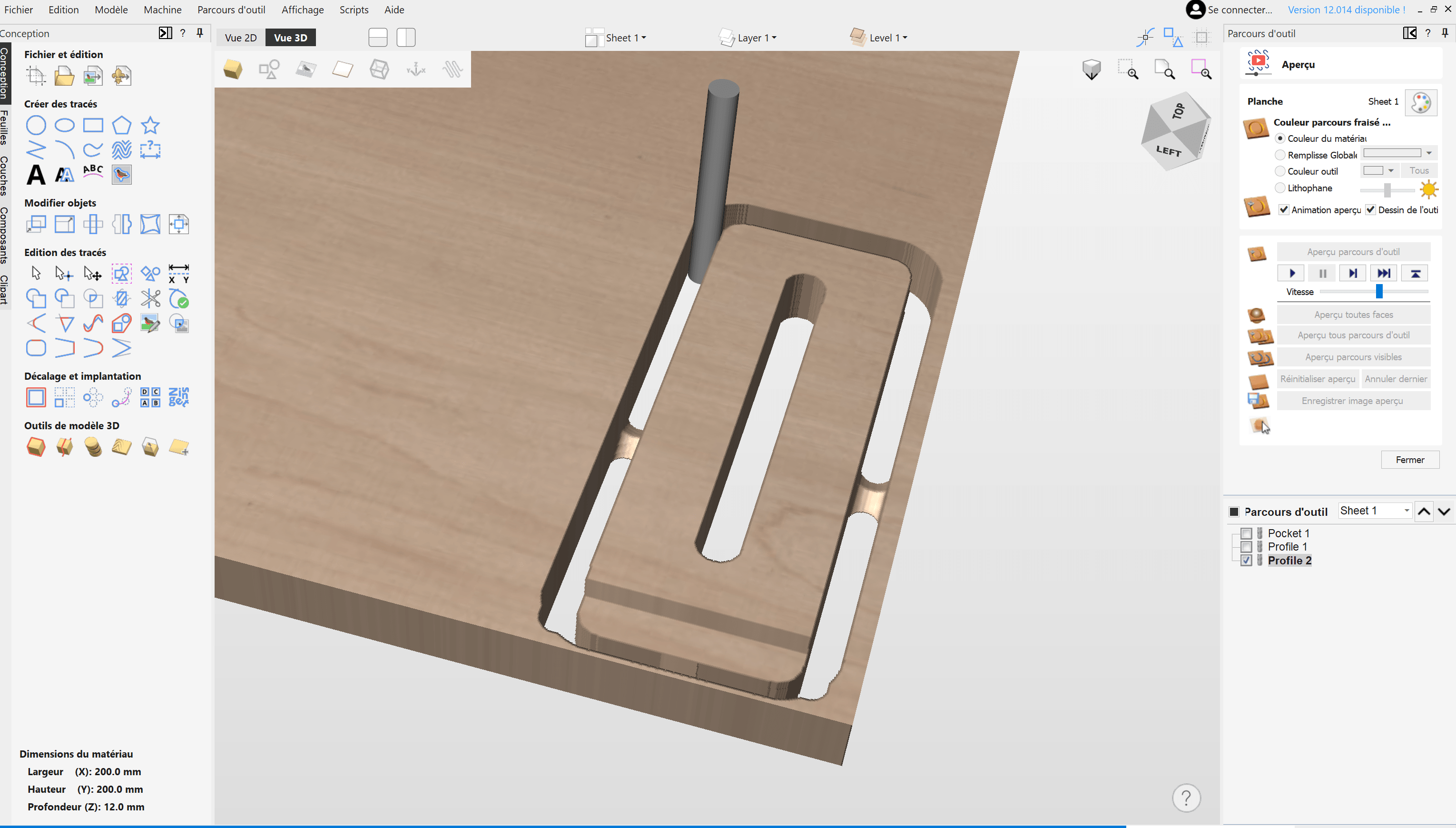
Apprenez comment créer votre projet et générer du G-Code à partir de VCarve Pro ou Aspire pour usiner facilement vos pièces sur une fraiseuse CNC.
Xavier K.
CNC Training
Lorsqu'il s'agit de travailler avec des matériaux de la taille d'un panneau, tels que le contreplaqué, le MDF ou les plastiques, les fixer avant de les usiner peut s'avérer être une tâche difficile et chronophage.
C'est là que la solution ingénieuse des tables à dépression rentre en jeu.
Les tables à dépression ont gagné en popularité en tant que solution de fixation pour les grandes fraiseuses numériques, et ce pour de bonnes raisons : elles offrent un niveau de facilité et de polyvalence difficile à égaler avec les méthodes de fixation traditionnelles.
Que vous soyez un professionnel chevronné de la CNC ou que vous fassiez vos premiers pas dans le monde de l'usinage CNC, il est essentiel de comprendre les avantages des tables à dépression pour exploiter pleinement le potentiel d’une fraiseuse CNC.
Dans cet article, nous décrirons la construction d'un système à dépression simple qui peut être installé sur notre modèle CNC Fab.
Nous expliquerons également les concepts clés qui vous aideront à comprendre les aspects les plus importants d'un système à dépression et vous guideront sur la manière d'adapter cette conception à votre propre installation.
Commençons par une brève explication de la physique du vide, qui nous aidera à comprendre comment optimiser notre conception.
La théorie ne vous intéresse pas ? Allez directement à la fabrication.
La pression atmosphérique standard au niveau de la mer est de 101325 Pa, soit plus ou moins 1 bar. Cette pression est générée par le poids de l'air qui nous entoure et qui peut varier en fonction de l'altitude et des conditions météorologiques. Pour créer un vide, il est donc nécessaire de générer une pression inférieure à la pression atmosphérique, dans un volume déterminé.
Les tables à dépression fonctionnent en utilisant cette différence de pression entre le vide sous une pièce et la pression atmosphérique au-dessus, générant ainsi une force de maintien.
Cette force est directement proportionnelle à la différence de pression et à la surface exposée. Par conséquent, les pièces de grande taille peuvent subir des forces de maintien importantes, tandis que les pièces de petite taille sont soumises à des forces de maintien plus faibles.
Prenons l'exemple suivant :
Dans ce cas-ci, nous avons une pompe à canal latéral qui peut générer une différence de pression de 250 mbar, sous une planche de contreplaqué de 50 cm x 50 cm. En calculant que la force est proportionnelle à la différence de pression et à la surface utile de vide, nous constatons que la pièce subira une force de maintien de 625 kg.
Pour savoir si cette force empêchera la pièce de bouger pendant un usinage, nous devons nous assurer que les forces de coupe restent inférieures aux forces de maintien agissant sur cette planche. Quatre forces sont en jeu :
Fh est la force de maintien créée par le vide + le poids de la planche. D'après la théorie du frottement statique, nous savons que cette force crée une force de frottement Ff qui empêche la planche de glisser lorsque la force de coupe radiale Fr agit sur elle.
Si une fraise "up cut" est utilisée, la force de coupe axiale Fa doit également être prise en compte (bien qu'elle soit souvent beaucoup plus faible que la force radiale, en fonction de l'angle d'hélice de la fraise).
Si la table à dépression et la planche sont tous deux en bois, le coefficient de frottement statique est de 0,40. En négligeant le poids du plateau, on obtient une force de frottement totale de :
Ff = µ x Fh = 0,40 x 6250 = 2500 N
Pour vous donner une comparaison (très) approximative, une fraise de 6 mm coupant dans du contreplaqué avec un engagement d'outil de 100 %, une profondeur de coupe de 6 mm et à 5 000 mm/min générerait une force de coupe radiale de l’ordre de 50 N. Comme vous pouvez le constater, il n'y a aucun risque de voir la pièce bouger pendant la coupe.
Il faut garder à l'esprit que la force de maintien calculée dans cet exemple reste une valeur théorique. Dans la pratique, il existe quelques facteurs qui peuvent réduire cette force, tels que :
En ce qui concerne ce dernier point, il faut toujours tenir compte du fait que la surface effective sur laquelle la force du vide agit ne s'applique qu'à la zone comportant des canaux ou des rainures.
Par conséquent, c'est la surface des canaux couverts et non la surface de la pièce réelle qui déterminera la force de maintien. Cette considération influencera la conception de notre table, comme vous le verrez plus loin.
Ok, assez de théorie, parlons pratique et découvrons comment mettre cela en œuvre sur notre fraiseuse CNC. En résumé, un système de fixation par dépression est composé des éléments principaux suivants :
Regardons à present les spécifications de chaque élément de ce système, afin de comprendre comment ils fonctionnent ensemble.
De nombreux types de machines peuvent être utilisés pour créer un vide, mais nous nous intéresserons ici principalement à deux types de machines :
Voici un tableau simplifié qui met en évidence les différences entre chaque type. La réalité est bien sûr plus nuancée, car il existe de nombreux modèles différents dans des gammes de prix très variées, mais ce tableau devrait vous donner une idée de ce que vous devriez rechercher lorsque vous concevez votre table aspirante.
|
Pompe à canal latéral |
Pompe à déplacement positif |
Capacité de débit d'air |
Haut |
Bas |
Niveau de vide |
Bas |
Haut |
Coût |
Abordable |
Elevé |
Durabilité |
Susceptible à la défaillance |
Plus robuste |
Grâce à leur grande capacité de débit d'air et à leur prix abordable, les pompes à canal latéral sont souvent la solution préférée pour les grandes fraiseuses CNC, car la taille des pièces à usiner compense les niveaux de vide inférieurs (rappelez-vous la formule : si la différence de pression diminue, la même force de maintien peut être appliquée si la surface de la pièce à usiner augmente).
Il faut cependant garder à l'esprit qu'elles sont parfois sujettes à des défaillances, généralement causées par des particules ou des copeaux qui pénètrent dans la chambre et bloquent la turbine. De même, si la circulation d'air est insuffisante, la turbine surchauffe et se dilate, ce qui entraîne une fusion potentielle avec le châssis et une défaillance catastrophique.
Il est donc fortement recommandé d'installer un filtre adéquat à l'entrée, ainsi qu'une valve de surpression qui permettra à un flux d'air minimal de circuler en permanence.
En revanche, les pompes à vide sont bien adaptées aux petites fraiseuses CNC,dont les pièces à usiner offrent une zone de vide plus petite. Elles tombent rarement en panne et représentent une solution rentable qui nécessite peu d'entretien.
Le plénum est une plaque rainurée comportant un ou plusieurs trous menant à la pompe à vide. Lorsque la pompe est mise en marche, un vide est créé à l'intérieur de ces canaux libres et tout matériau placé au-dessus est aspiré vers le bas. Pour éviter les fuites et la perte de performance du vide créé, un joint en caoutchouc soupleest souvent placé à l'intérieur des rainures sur le périmètre de la pièce à usiner.
Vous pouvez voir dans cette conception que la zone de vide effective a été optimisée sans compromettre la rigidité de l'ensemble de la planche, en utilisant un motif en croix sur chaque carré de maintien. Cela permet d'augmenter considérablement la force de maintien.
Pour canaliser le flux d'air vers notre pompe, il existe plusieurs possibilités. La première consiste à utiliser des tuyaux flexibles et des connecteurs pneumatiques. Cette méthode s'avère efficace et facilite un processus d'installation rapide et simple.
Si cette approche est idéale pour les petites tables à dépression, la prudence est de mise pour les systèmes à vide plus importants, car le faible diamètre des tuyaux limitera le débit d'air.
Pour les tables aspirantes de plus grande taille, il est recommandé d'utiliser des tuyaux en PVC et leurs connecteurs standard. Il s'agit d'une solution simple et peu coûteuse, avec des pièces que l'on peut trouver dans n'importe quelle quincaillerie.
En outre, lors de la conception d'une table plus grande, il convient d'envisager la création de plusieurs zones. Cela peut se faire en utilisant des bouchons étanches pour chaque zone, ou en ayant des vannes qui permettront d'ouvrir ou de fermer facilement chacune d'entre elles avant un travail.
Le système d'aspiration complet se termine souvent par une plaque martyr en MDF qui vient s'ajouter sur le plenum. L'avantage de cette approche est double
Tout d'abord, il protège la partie coûteuse de la table à dépression de toute erreur d'usinage, car il est plus facile de remplacer un panneau MDF qu'un plenum usiné. D'autre part, il empêchera la poussière et les copeaux de pénétrer dans la pompe à vide.
Deuxièmement, le MDF étant un matériau poreux, le panneau répartira le vide des canaux uniformément sur toute la surface. Ainsi, la surface effective sur laquelle la dépressionest appliquée est plus grande, ce qui génère une force de maintien plus importante.
Bien que cette méthode s'avère efficace, il est important de comprendre qu'elle nécessite une pompe capable d'extraire un plus grand volume d'air, car le martyr laissera échapper de l'air de toute zone qui n'est pas recouverte par la pièce à usiner.
Pour illustrer ce point, examinons la courbe de performance d'une pompe à canal latéral de 1,5 kW, qui représente le différentiel de pression atteint en fonction du débit d'air.
On constate immédiatement que la dépression est inversement proportionnel au débit d'air. Supposons que notre martyr en MDF fuit 90 m³/h, la différence de pression disponible n'est alors que de 150 mbar, contre 285 mbar avec un vide parfaitement étanche, ce qui génère presque deux fois moins de force !
Bien entendu, il est également possible de combiner les deux techniques, en plaçant un cordon d'étanchéité sous le martyr aux dimensions exactes de votre pièce, afin de contenir la zone de vide et d'éliminer une grande partie des fuites.
La construction de cet article est destinée à fournir une table à dépression bon marché mais performante pour une fraiseuse numérique de taille panneau. Pour des raisons de budget, certaines améliorations ergonomiques mentionnées plus haut ont été laissées de côté, mais n'hésitez pas à les ajouter à votre propre installation.
Nous avons décidé de travailler avec deux pompesà canal latéral de 2,2 kW qui seront connectées en parallèle, ce qui nous permettra d'avoir une plus grande capacité de débit d'air et de maintenir un vide important.
Cette solution est également moins coûteuse que l'achat d'une pompe plus grande et plus puissante, et nous permet de rester dans la gamme des moteurs monophasés (les pompes à canal latéral plus grandes nécessitent la plupart du temps une sortie triphasée). Si votre budget le permet, envisagez d'acheter une pompe de chez Black Box Vacuum, qui offre un excellent rapport qualité/prix.
Le plénum sera fabriqué à partir des martyrs MDF standard de notre catalogue pour CNC Fab, car ils sont peu peu coûteux et modulaires (une seule pièce peut être remplacée en cas d'endommagement). Mais bien sûr, vous pouvez aussi utiliser un panneau entier pour fabriquer la table, il vous suffira d'adapter le G-code fourni (lien vers le projet Fusion360 ci-dessous).
Si vous souhaitez opter pour une version plus haut de gamme, nous vous recommandons d'utiliser des panneaux plastiques en PLA ou en nylon, car ils sont faciles à usiner et permettent d'obtenir un plénum très stable.
La plupart du temps, il est souhaitable de commencer l’usinage du plénum par une opération de surfaçage, car cela permet de niveler parfaitement la zone de travail. Nous avons décidé de l'éviter et de faire simple ici, car la couche supérieure du MDF n'est pas aussi poreuse que son intérieur.
Cela nous évite de surfacer et de devoir appliquer un produit composite sur toute la surface supérieure de notre plénum pour le rendre étanche à l'air (cela ne s'applique pas si vous utilisez un autre matériau que le MDF, bien entendu). Le niveau parfait sera réalisée ultérieurement à l'aide d'un martyr surfaçé.
Si vous souhaitez néanmoins effectuer un surfaçage, utilisez un produit d'étanchéité pour bois sur la surface usinée et appliquez-en également sur les côtés du panneau, afin de réduire encore davantage les fuites. Dans ce cas, nous recommandons également d'utiliser des panneaux plus épais, afin de conserver une rigidité suffisante même après avoir enlevé du matériau (des panneaux de 25 mm au lieu de 18 mm seraient une bonne option, par exemple).
Comme nous venons de l'expliquer, nous utiliserons un fin panneau en MDF au-dessus du plenum, qui fera office de martyr et empêchera la table d'être endommagée si l'outil descend trop bas au cours d'un usinage.
Nous utiliserons également un cordon en néoprène sur le plénum pour définir précisément les zones où le vide doit être appliqué et obtenir un bon effet d'étanchéité. Cela permet d'utiliser des pompes moins performantes tout en obtenant de bons résultats.
Enfin, nous utiliserons des vannes à tiroir pour ouvrir/fermer 4 zones définies sur le plénum. Là encore, cela nous permet d'optimiser la zone de vide effective lorsque nous ne fraisons pas un panneau entier.
Cette section fournit un guide étape par étape sur la fabrication du plénum de notre système d'aspiration et sur la mise en œuvre d'un réseau de tuyauterie complet avec 4 zones.
Voici les liens importants dont vous aurez besoin pour cette construction :
C'est parti !
Vérifiez que le bâti de la table de la machine est bien nivelé. Vous devez disposer d'une bonne surface de travail plane pour bien commencer, d'autant plus que nous ne surfacerons pas le plénum.
Fixez les quatre parties du spoilerboard. Assurez-vous qu'elles sont bien alignées et que chaque vis est bien serrée.
Allumez votre machine et attendez que PlanetCNC se charge.
Faites un “Home” de la machine et un “Square” du portique.
Sans changer la position de la machine, entrez les coordonnées de travail suivantes : (X73.5 ; Y66)
Insérez une fraise plate de 8mm (3 dents dans notre cas), et laissez la dépasser de 40mm pour permettre à la machine de fraiser jusqu'en dessous du plenum, sinon la machine enverra un message d'erreur de limite machine.
Utilisez le palpeur de l'axe Z pour mesurer la longueur de l'outil et mettez l'axe à zéro sur la surface supérieure du plénum
Mettez la botte d’aspiration.
Chargez le G-code et démarrez le programme.
Lorsque les 4 trous sont fraisés, la machine s'arrête pour un changement d'outil. Remplacez l'outil actuel par une fraise plate de 5 mm (à deux dents dans notre cas).
N'oubliez pas d'effectuer une nouvelle mesure de l'outil pour recalibrer le Z0.
Appuyez sur le bouton pause pour continuer le programme.
Lorsque le programme est terminé, déplacez le portique à l'arrière de la machine. Poncez délicatement les bords de la coupe avec du papier de verre fin et nettoyez l'ensemble du plénum à l'aide d'un aspirateur.
Commencez par ouvrir l'assemblage 3D de l'ensemble du système pour comprendre comment tout sera connecté.
Le système de tuyauterie consiste en un réseau de tuyaux en PVC de 63 mm, normalement utilisés pour l'évacuation de l'eau. Vous pouvez utiliser des tuyaux à pression PN10 ou PN16 si vous le souhaitez, mais cela ajoutera un coût inutile à votre assemblage.
Les zones seront activées à l'aide de vannes de 63 mm, qui seront toutes reliées entre elles par un collecteur de 90 mm. Ce collecteur est constitué de quatre tés de 90 mm raccordés contenant une réduction de 90-63 mm à leur sommet.
Tout d'abord, vous devez couper les tuyaux en PVC de 63 mm aux dimensions nécessaires :
Une fois cela fait, utilisez une ponceuse à bande pour créer un léger chanfrein de chaque côté des tuyaux qui ont été coupés. Poncez ensuite les surfaces qui doivent entrer en contact lors de l'assemblage, tant sur le tuyau mâle que sur le connecteur femelle.
Lorsque vous avez terminé, soufflez entièrement les tuyaux pour enlever la poussière sur toutes les faces, mais aussi à l'intérieur (vous ne voulez pas que cette poussière se retrouve dans votre système d'aspiration par la suite).
Vous aurez maintenant besoin d'un pistolet à calfeutrer avec de la colle universelle pour fixer les quatre tuyaux en PVC de 140 mm sur le plénum, créant ainsi la sortie pour chaque zone.
Mettez de la colle sur le tuyau en PVC et sur la surface intérieure des trous du plenum. Insérez ensuite chaque tuyau en PVC dans chaque trou, en veillant à ce qu'il affleure les rainures du caisson. Laissez sécher pendant plusieurs heures, comme indiqué sur le mode d'emploi de la colle. Cela permettra de créer une liaison solide et étanche à l'air.
Pendant que la colle sèche, commencez à assembler le réseau de tuyaux. Avant d'appliquer la colle PVC, essayez d'assembler tout à sec pour vous assurer que tout s'emboîte et que tout est à la bonne longueur. Vous pouvez également utiliser un marqueur pour marquer la profondeur d'emboîtement des tubes mâles dans les raccords coudés femelles, mais aussi pour vous assurer que vous avez des angles de 90° partout.
Lorsque vous êtes prêt, appliquez la colle PVC à l'aide d'un petit pinceau sur chaque tuyau et raccord, un par un. Assemblez d'abord les pièces intermédiaires, avant de les coller sur la sortie du plénum, cela vous facilitera la tâche.
Pré-assemblez également le collecteur, car il sera plus facile de le fixer au châssis de la machine.
Enfin, raccordez les sorties de chaque zone avec les tuyaux et les vannes pré-assemblés. Il se peut que vous deviez soutenir les deux tuyaux les plus longs à l'aide de colliers fixés au châssis de la machine, comme sur la photo ci-dessous.
Pour fixer le collecteur au châssis de la machine, vous devrez également utiliser des colliers de serrage de 90 mm. Ensuite, vous pouvez coller les dernières parties, le collecteur et la vanne de chaque zone.
La procédure à suivre pour cette étape dépend fortement du type de pompe dont vous disposez. S'agit-il d'une seule unité connectée directement au collecteur ou de plusieurs en parallèle (ou en série), quel est le diamètre d'entrée, avez-vous besoin de raccords filetés ? Nous n'entrerons donc pas dans les détails de cette partie de la construction..
Dans notre cas, nous avons décidé d'utiliser deux pompes à canal latéral à double étage, monophasés et d'une puissance de 1,5 kW. Nous les avons connectés en parallèle pour maximiser le débit d'air disponible.
Pour créer un martyr bon marché et ergonomique, nous avons décidé d'utiliser un panneau de MDF standard de 6 mm et de le découper en 4 parties égales, une pour chaque zone..
Pour usiner chaque plaque, nous allons utiliser notre nouvelle table à dépression pour la première fois ! Nous voulons enlever 1,5 mm de chaque côté pour obtenir des plaques de 3 mm.
Insérez un cordon de néoprène dans les rainures du plénum pour créer un joint d'étanchéité au périmètre de chaque panneau MDF, sur chaque zone..
Placez ensuite les 4 panneaux sur chaque zone et mettez les pompes en marche. Vous pouvez maintenant commencer l'opération de surfaçage (n'oubliez pas d'utiliser une botte d’aspiration !).
Une fois l'opération terminée, retournez les planches et répétez la même opération de l'autre côté. Après un nettoyage rapide à l'aspirateur, voici le résultat :
Revenons à notre exemple d'une plaque de contreplaqué de 50 x 50 cm avec une différence de pression de 250 mbar (obtenue sur nos pompes en utilisant un cordon d'étanchéité). En tenant compte d'une surface de vide effective de 50 %, la planche subira une force de retenue d'environ 300 kg.
Comme elle est placée sur une autre surface en bois, la force de frottement statique qui l'empêche de bouger est d'environ 120 kg.
Nous avons utilisé un simple dynamomètre pour vérifier que la planche ne bougeait pas. Nous n'avions pas assez de force pour tirer 120 kg, mais nous avons réussi à mesurer une force de 50 kg et effectivement, la planche n'a pas bougé du tout.
Satisfaits de ce résultat, nous avons décidé de placer une planche de pin plus petite sur la table à dépression (cette fois-ci, en utilisant également le martyr avec le cordon d'étanchéité) et d'utiliser une fraise à surfacer de 25 mm. L'opération s'est déroulée sans problème, avec très peu de vibrations de la planche car elle était très bien maintenue, malgré sa petite taille.
Voilà, vous êtes arrivé à la fin de ce long article !
Nous espérons qu'il vous a été utile et qu'il vous a inspiré pour créer votre propre système d'aspiration. N'hésitez pas à partager votre expérience avec nous, ou simplement à nous contacter si vous avez des commentaires ou des remarques.
Mekanika est une entreprise belge basée à Bruxelles dont l'ambition est de rendre la production locale plus accessible grâce à une approche 100% open-source.
Nous concevons et produisons des machines de haute qualité pour le fraisage CNC et la sérigraphie, qui ont été reconnues pour leur fiabilité et leur facilité d'utilisation. Nos outils sont livrés en kits et entièrement documentés, permettant facilement de les adapter à des besoins spécifiques.
Visitez notre boutique pour en savoir plus, ou consultez notre ressources en ligne et tutoriels pour continuer à apprendre.
Apprenez comment créer votre projet et générer du G-Code à partir de VCarve Pro ou Aspire pour usiner facilement vos pièces sur une fraiseuse CNC.
Xavier K.
CNC Training
Gravure à chaud, gravure à froid, outils et tutoriels : tout ce que vous devez savoir sur comment utiliser votre fraiseuse pour faire de la gravure CNC sur bois.
Quentin L.
Content Creation
Apprenez comment créer votre projet et générer du G-Code à partir de Carveco pour usiner facilement vos pièces sur une fraiseuse CNC.
Quentin L.
Content Creation