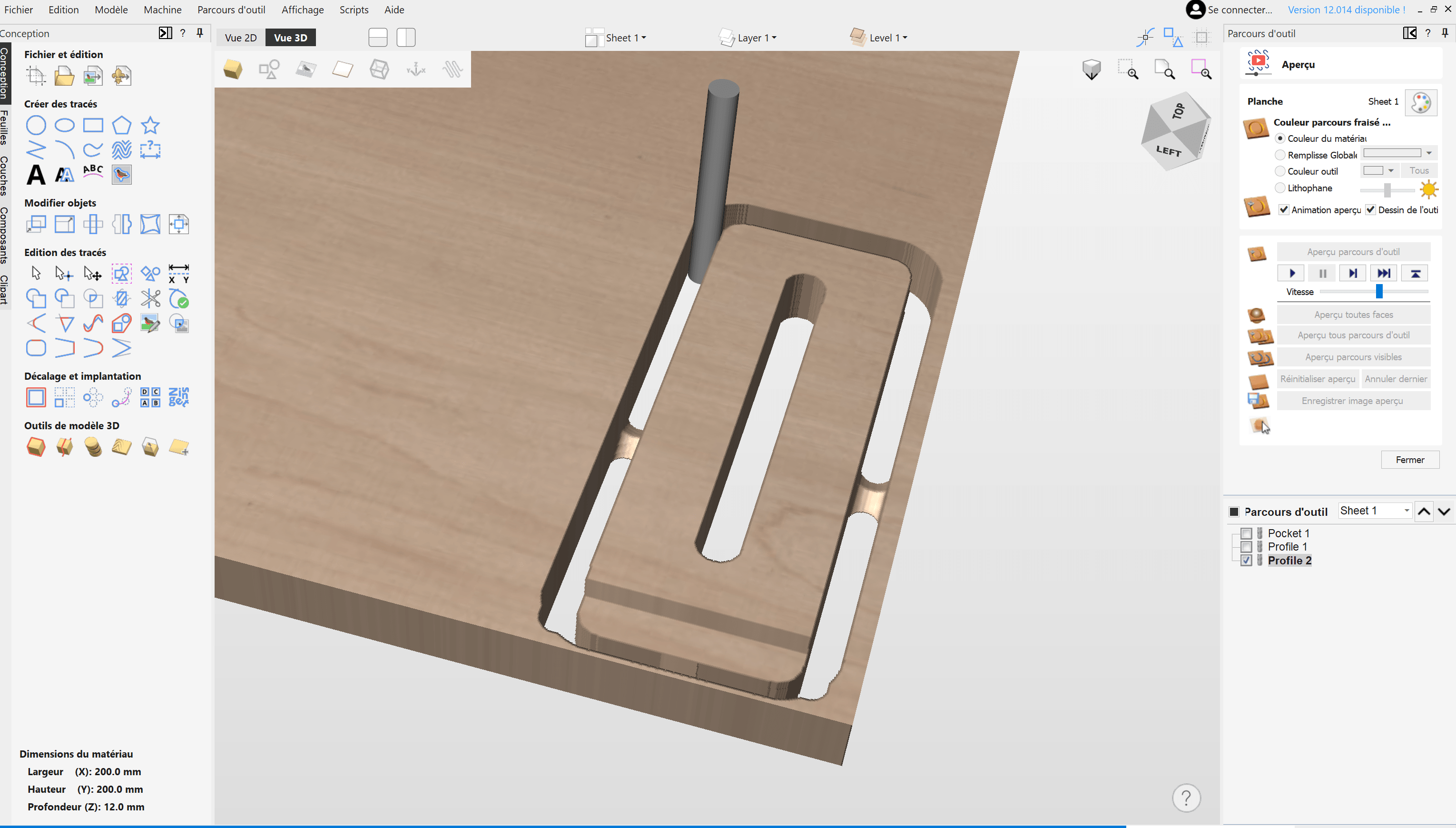
Apprenez comment créer votre projet et générer du G-Code à partir de VCarve Pro ou Aspire pour usiner facilement vos pièces sur une fraiseuse CNC.
Xavier K.
CNC Training
Maintenant que votre machine est installée et que vous l'avez testée en découpant les pinces ou autres fichiers disponibles sur notre site, il est temps de créer votre propre fichier de découpe. Il existe plusieurs possibilités, et dans cet article, nous allons simplifier les choses au maximum, afin que même si vous êtes novice en matière de fraisage CNC, vous puissiez vous lancer en un clin d'œil !
Nous verrons ici comment importer un fichier DXF dans PlanetCNC.
Vous avez une idée très précise de ce que vous souhaitez découper ? Pour commencer, pas de fioritures, choisissez une forme simple et sans reliefs comme cet hippocampe dont nous allons découper les contours.
Avant tout, il va falloir vectoriser cette forme, les vecteurs donneront les coordonnées dont la machine a besoin pour ce guide.
Une solution consiste à utiliser un logiciel de dessin 2D comme Illustrator, Inkscape ou encore Corel Draw. Si vous débutez dans le dessin vectoriel, vous pouvez dessiner sur papier, scanner puis importer le tout dans le logiciel de dessin et en redessiner les contours
Ensuite, enregistrer votre fichier au format DXF.
Vous pouvez télécharger le fichier que nous avons utilisé pour cet article ici.
Note : pas encore à l’aise avec la vectorisation ? Vous pouvez acheter des DXF tout prêt sur des plateformes comme Etsy, par exemple.
La qualité de votre fichier vectoriel influencera fortement la qualité de votre découpe. Un tracé propre se traduira par un parcours machine propre.
Comme vous le savez, Planet CNC est le logiciel de contrôle que nous avons choisi pour piloter nos machines. Il est capable, à partir d’un DXF de générer un Gcode que votre machine pourra lire pour usiner vos découpes. Nous vous invitons à lire ces deux articles pour acquérir les fondements du contrôle logiciel langage spécifique au fraisage numérique.
Pour importer le DXF, sélectionnez Dossier > Importation DXF
Une fenêtre s’ouvre alors avec différentes possibilités de réglages. Nous allons vous indiquer la marche à suivre pour pouvoir rapidement découper votre premier contour.
Choisissez l’unité (Units) dans laquelle vous souhaitez travailler, ici, nous choisissons les mm.
Veillez à bien contrôler l’échelle indiquée à chaque importation de DXF, surtout si vous avez l’habitude de modifier cette donnée, car les choix sont sauvegardés d’une importation à l’autre.
Pour positionner le DXF dans l’espace de travail de la machine, nous avons 5 choix d’origine dans Origin. Cochez la case en bas à gauche.
Le Gcode ne doit être lu qu’une seule fois, entrez le chiffre 1 dans le champ de Boucle (Loops).
Pour générer le parcours d’outils, cliquez ensuite sur « Path » (chemin). La fraise sera ainsi centrée sur le tracé.
Concernant le diamètre de l’outil choisi : il est possible d’utiliser le champ offset pour le paramétrer. L’offset peut être positif ou négatif.
Le tracé sera ainsi grossi ou au contraire aminci. La fraise venant se placer pile sur le tracé, l’offset permet à l’outil de retirer ce qu’il faut de matière au bon endroit pour que la forme garde son aspect initial.
Une fois le chemin de coupe et l’outil définit en x et y, passons aux paramétrages en z. Pour cela, il faudra renseigner toutes les infos dans la partie « Height » (hauteur). Avant cela, cochez le Mode 2D qui permet d’accéder à tous les paramètres de hauteurs.
Planet CNC calculera combien de passes seront nécessaires pour arriver à la profondeur de coupe demandée.
Il est tout à fait possible de « penser » dans l’autre sens, à savoir, indiquer 0 pour la hauteur de départ, -1 pour la profondeur de passe et -3 pour la profondeur de coupe maximum. La coupe sera la même, seul le gcode sera différent avec des valeurs négatives en Z. Faites attention à l'endroit où vous effectuez votre repère Z lorsque vous choisissez une direction de coupe. Dans le cas de valeurs Z négatives, elle doit être effectuée sur le dessus de la pièce.
Il est possible de paramétrer des onglets pour, qu’une fois découpée, votre pièce ne se détache et soit projetée dans votre atelier.
Dans l’espace « Tabs », il est possible de définir la distance entre deux onglets et la taille de ceux-ci, mais il n’est malheureusement pas possible de choisir leurs emplacements. Ici, nous avons choisi une distance de 50 mm et une taille de 2 mm, les onglets se placent ensuite automatiquement.
Dernier maillon des réglages de coupe, il faut donner nos indications concernant les vitesses de travail.
Vous trouverez un article sur notre blog pour en savoir plus sur les vitesses de coupe et d'avance.
Dans la partie « Outputs », cochez la case « Spindle » (broche) et indiquez 20.000 dans le champ vitesse. Votre broche tournera ainsi à 20 000 tr/min.
Enfin, les dernières lignes de la fenêtre d’importation des DXF sont réservées au pilotage de l’allumage et de l’extinction de la broche, mais également d’un éventuel flux d’eau pour la découpe d’autres matériaux que le bois. Vous avez plusieurs options :
Pour ce qui est de la broche, nous vous conseillons de ne rien paramétrer ici. En effet l’allumage et l’arrêt de l’outil se feront automatiquement aux moments opportuns si vous laissez toutes les cases décochées.
Maintenant que tout est paramétré, cliquez sur OK, votre fichier est prêt à être usiné. Vous découvrez à l’écran le chemin de l’outil et les différentes passes de découpe. Il ne vous reste plus qu'à attacher votre pièce, faire les procédure de positionnement et de sécurité et lancer votre usinage !
Bonne découpe !
Voici un récapitulatif des avantages et des inconvénients de travailler directement avec des fichiers vectoriels sur vos machines CNC.
Les avantages sont :
Les désavantages sont :
Mekanika est une entreprise belge basée à Bruxelles dont l'ambition est de rendre la production locale plus accessible grâce à une approche 100% open-source.
Nous concevons et produisons des machines de haute qualité pour le fraisage CNC et la sérigraphie, qui ont été reconnues pour leur fiabilité et leur facilité d'utilisation. Nos outils sont livrés en kits et entièrement documentés, permettant facilement de les adapter à des besoins spécifiques.
Visitez notre boutique pour en savoir plus, ou consultez notre ressources en ligne et tutoriels pour continuer à apprendre.
Apprenez comment créer votre projet et générer du G-Code à partir de VCarve Pro ou Aspire pour usiner facilement vos pièces sur une fraiseuse CNC.
Xavier K.
CNC Training
Gravure à chaud, gravure à froid, outils et tutoriels : tout ce que vous devez savoir sur comment utiliser votre fraiseuse pour faire de la gravure CNC sur bois.
Quentin L.
Content Creation
Apprenez comment créer votre projet et générer du G-Code à partir de Carveco pour usiner facilement vos pièces sur une fraiseuse CNC.
Quentin L.
Content Creation