Pack Content
Basic End Mills Starter Pack (with or without collets)
- 1x Carbide 3-flute flat endmill 8mm, multi material - Ø=8.0mm - D=8.0mm - L=20mm
- 2x Carbide 3-flute flat endmill 6mm, multi material - Ø=6.0mm - D=6.0mm - L=15mm
- 1x Carbide 2-flute flat endmil 3mm, multi material - Ø=3.0mm - D=3.175mm - L=15mm
- 1x Carbide 2-flute flat endmill 3mm, aluminium - Ø=3.0mm - D=3.175mm - L=10mm
- 1x Carbide 2-flute downcut endmill 3mm, multi material - Ø=3.0mm - D=3.175mm - L=8mm
- 1x Carbide 45° engraving endmill, multi material - D=3.175mm
- Optional: 2x Collets, diameters 3,00mm & 6,00mm (ER16 or AMB - only for packs with collets)
Ø = cutter diameter - D = shank diameter - L = flutes length)
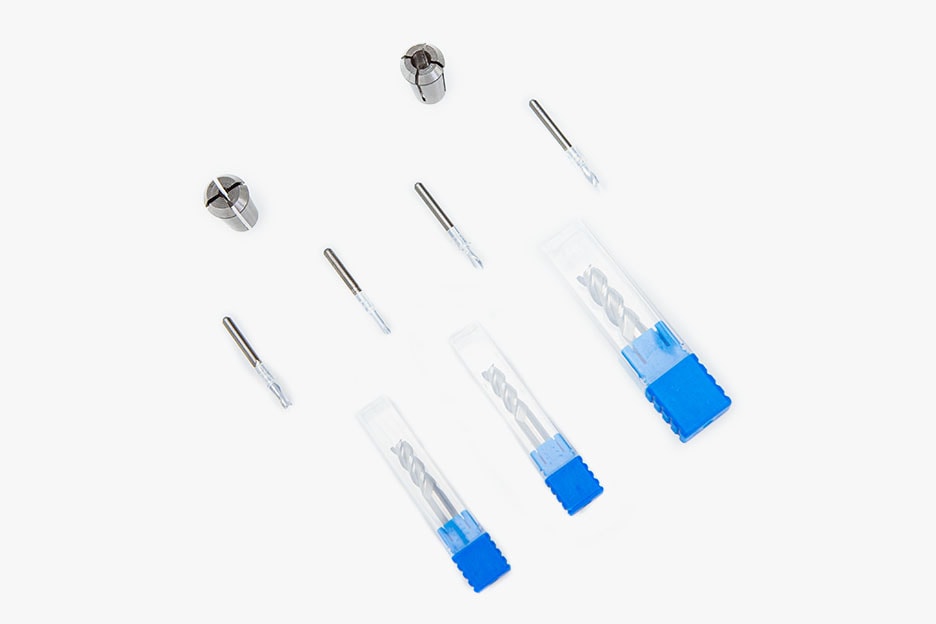
Fraiser Poly Kit
You will get the following end mills made by Fraiser, all shipped together in individual protective packages:
- 1x A212.060.6D, a V-cut engraving cutter, 60°, for applications in plastics, plexiglass and light alloys such as aluminium and copper.
- 1x A304.031.6D, a 3mm one-flute milling cutter for cutting plastics and derivatives.
- 1x A302.030.6D, a 3mm one-flute milling cutter for cutting aluminium and light alloys.
- 1x A303.030.6D, a 3mm downcut one-flute cutter. Thanks to the negative pushing helix, it allows you to mill sheets with small thicknesses without getting too much vibration.
All the end mills have a 3mm cutting diameter (except for the 60° bit) and a 6mm shank diameter.
WARNING: Collets are not provided in the kits
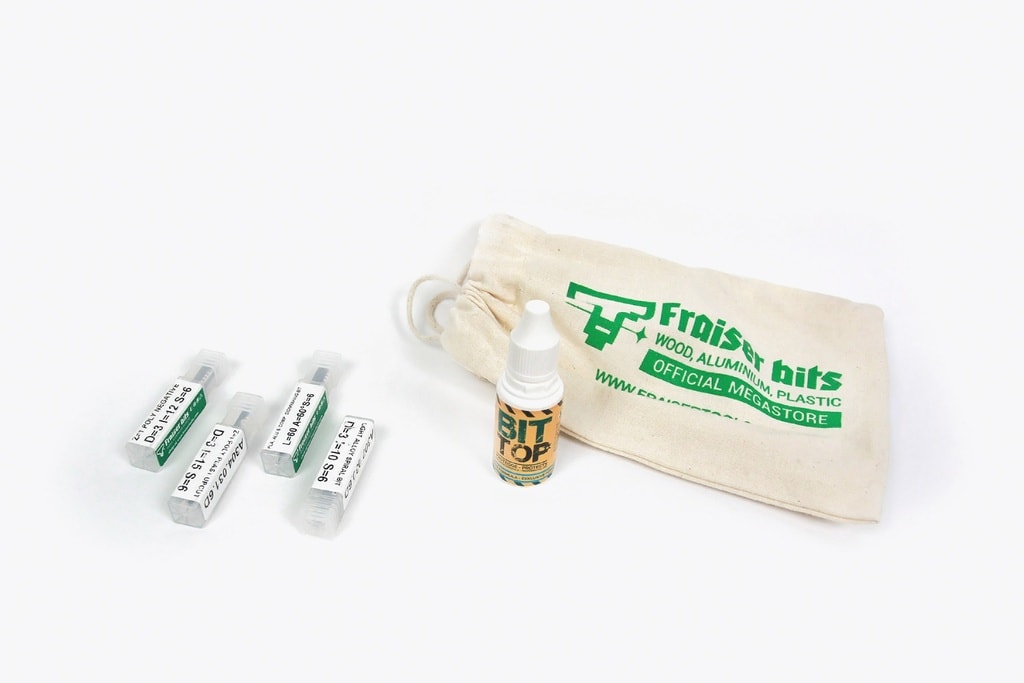
Fraiser Boss Complete Set
You will get the following end mills made by Fraiser, all shipped together in individual protective packages:
- 1x P302.060.6D, a 6mm upcut milling cutter with 2 positive helical cutting edges.
Diameter 6mm, cutting height 17mm, with high chip discharge - 1x P303.060.6D, a 6mm downcut milling cutter for grooves on coated or delicate materials, 2 negative cutting helixes that push the chips down leaving the top of the workpiece perfect.
Diameter 6mm, cutting height 27mm. - 1x P313.060.6D, a 6mm ball nose milling cutter with a 3mm cutting radius and 2 positive helical edges, for any 3D operation or rounded grooves,
- 1x P212.060.6D, a 35° single flute lettering and engraving cutter for fine detailed engravings.
Shaft diameter: 6mm
WARNING: Collets are not provided in the kit
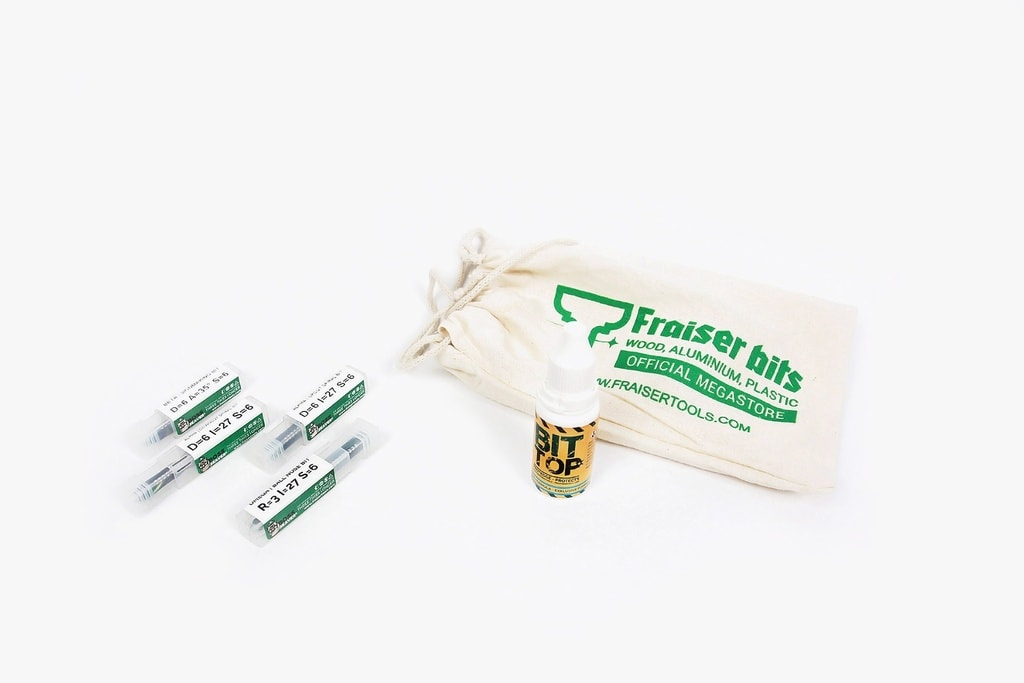
Fraiser Boss Ultimate Set
You will get the following end mills made by Fraiser, all shipped together in individual protective packages:
- 1x P302.060.6D, a 6mm upcut milling cutter with 2 positive helical cutting edges.
Diameter 6mm, cutting height 17mm - 1x P303.060.6D, a 6mm downcut milling cutter with 2 negative cutting helixes that push the chips down leaving the top of the workpiece perfect.
Diameter 6mm, cutting height 27mm. - 1x P307.080.8D, a 8mm roughing milling cutter with 3 chip breaker flutes, that crushes even the hardest wood with ease and allows you to move quickly into the workpiece.
Diameter 8mm, cutting height 35mm. - 1x P212.060.6D, a 35° single flute lettering and engraving cutter for fine detailed engravings.
Shaft diameter: 6mm - 1x P301.031.6D, a 3mm upcut 1 flute milling cutter perfect for plastics.
Cutting diameter 3mm, Shaft diameter 6mm, Cutting height 12mm - 1x P314.032.6D a tappered ball nose end mill with 3 upcut flutes, that pull the chips upwards and have a conical profile that allows you to create 3D millings.
Shaft diameter 6mm, Tapper Angle 2.5° , Tip radius 1,6mm
WARNING: Collets are not provided in the kit
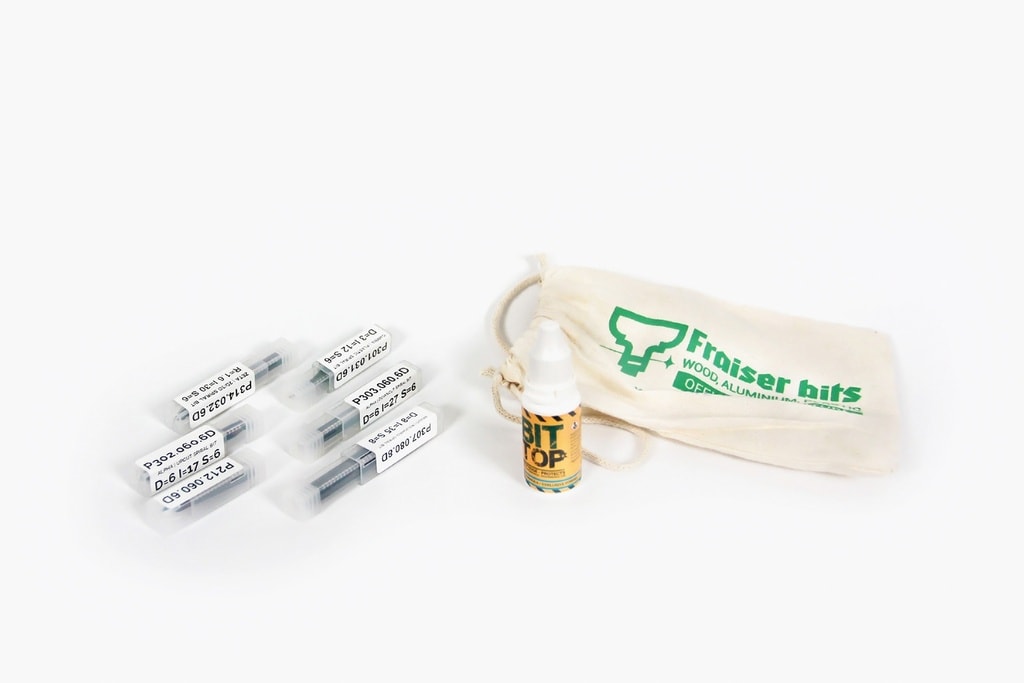
Tools Parameters
We provide a pre-configured library of tools for Fusion360, which will help you get the optimized cutting parameters for these end mills. For those of you that use a different CAM environment. The zip archive contains a text file with all the cutting parameters as well.
Note: Considering that your machine, your end mill stick out, and the material used will be in different conditions than the ones used to determine the parameters, we recommend you use the parameters as ideal values to be reached gradually. Always start with slightly lower values and gradually increase, being ready to intervene if the milling should proceed in the wrong way. We decline all responsibility for the results obtained. Also note that if you are working against the grain of wood, the indicated feed rate values should be multiplied by 0.7. The same factor should be applied if working on Evo, since the machine is less rigid than the Pro and Fab models.