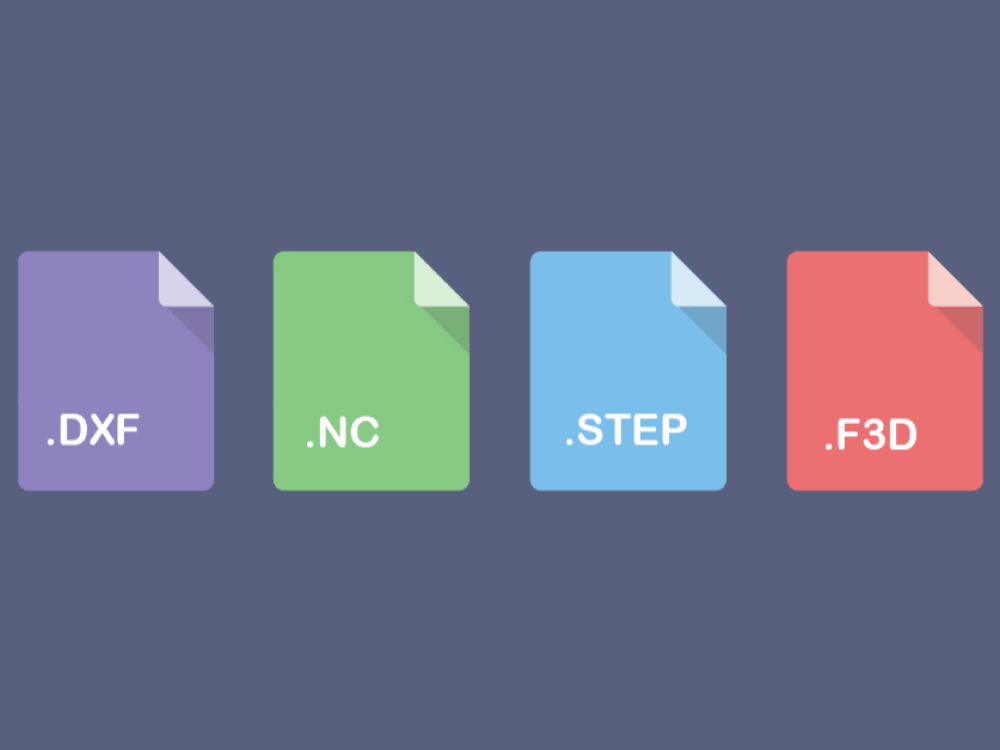
With this guide, discover how to use your DXF or STEP files and convert them. We deal with most frequent issues faced when learning CNC milling.
Roldan D.
Sales & Marketing
Are you learning CNC milling? Here are some tips and tricks to improve and optimize the use of your CNC machine, from work preparation to end mill selection.
90% of the machining errors we make in the workshop are due to a lack of attention: even being experienced, urgency regularly makes us forget certain last-minute checks.
However, this very simple advice can save you a lot of time (and money if you count the waste of material during unsuccessful machining): take your time and check your file and installation before starting.
You can also check our poster "Ready To Mill?" that will help you to validate all the steps before launching your program!
Every time you start with a new material or operation, first perform your feeds & speeds calculations.
This will give you a reference value to start working with this new material. Then be conservative at first and push your machine gradually as you master the operation.
You will make fewer mistakes and be able to get the most out of your machine's capabilities.
Each material or operation requires a suitable end mill, whether you want to perform cutting, engraving, tapping, or surface milling. Be sure to use an end mill dedicated to the material and operation you intend to perform.
Also try to minimize your working time:
Careful, if you're a beginner, you'll break end mills, it's inevitable.
This advice applies only when you have mastered a minimum of milling.
Although it's tempting to get cheap milling cutters online (we're not going to lie, we've done it regularly), it's rarely a winning bet: you end up missing works, changing tools regularly or even having bits whose parameters are not rigorously accurate (a small variation in size can quickly make all the difference).
Make sure you have end mills with good references and made of resistant materials with quality coatings.
We recommend end mills from Fraiser Tools.
Although there are relatively few problems related to chip evacuation when cutting wood, good evacuation becomes crucial when dealing with materials such as plastics or metals.
An end mill that cuts into chips - and melts them - is one of the main causes of tool breakage in milling. So make sure you have the right chip evacuation system:
There are many ways to fix parts on a digital milling machine, sometimes more or less flexible, sometimes faster or slower.
Take the time to experiment with several spoilerboards and clamping systems until you find the one that suits you best. This will allow you to have your system in mind when designing your parts and will save you precious time.
In the obvious list of tips, this one comes in a good place. However, it is easy to put off cleaning your machine after a successful milling job.
Good maintenance will allow you to maintain the precision of your machine for longer and to spot problems in time. It will also give you peace of mind when you start your next milling job.
To properly maintain your machine, consider :
It is quite easy to master the basics of a CAD/CAM software such as Autodesk Fusion 360.
In less than a week and without any prior knowledge, you can be able to draw simple parts in 3D and generate the milling files to manufacture them.
But keep in mind that these software programs are extremely powerful and allow you to optimize your milling time, improve your finishes or increase the capabilities of your machine almost infinitely.
Don't rest on your laurels and take the time to always learn and learn more about these software programs.
Our tip: In parallel with your work, take the time to set yourself a new goal each week to test new functions.
Although it is no longer necessary today to control your machine manually by injecting lines of code, knowing the basics of G-code will allow you to master it in depth by controlling it directly from your control software.
You will also be able to find yourself in the many lines of code of a milling machine if you have had to stop along the way, or even spot an error in order to correct it.
You can learn more on the topic with our G-code guide.
Your machine's control software can also be very powerful and full of options that will make your job easier.
For example, PlanetCNC includes a live DXF file importer, allowing you to switch directly from Illustrator to milling without having to use CAM software. It also includes options to speed up series production. The graphical user interface also includes many speed control or setting options that can be useful.
Take the time to read the associated documentation and refine your knowledge of the software.
Mekanika is a Belgian company based in Brussels whose ambition is to make local production more accessible thanks to a 100% open-source approach.
We design and produce high quality machines for CNC milling and screen printing, which have been recognized for their reliability and ease of use. Our tools are delivered as kits and fully documented, allowing to easily adapt them to specific needs.
Visit our shop to find out more, or check out our online resources and tutorials to continue learning.
With this guide, discover how to use your DXF or STEP files and convert them. We deal with most frequent issues faced when learning CNC milling.
Roldan D.
Sales & Marketing
Learn how to create your project and generate G-Code from VCarve Pro or Aspire to easily machine your parts on a CNC milling machine.
Xavier K.
CNC Training
Hot engraving, cold engraving, tools and tutorials: everything you need to know about wood engraving with your CNC machine.
Quentin L.
Content Creation