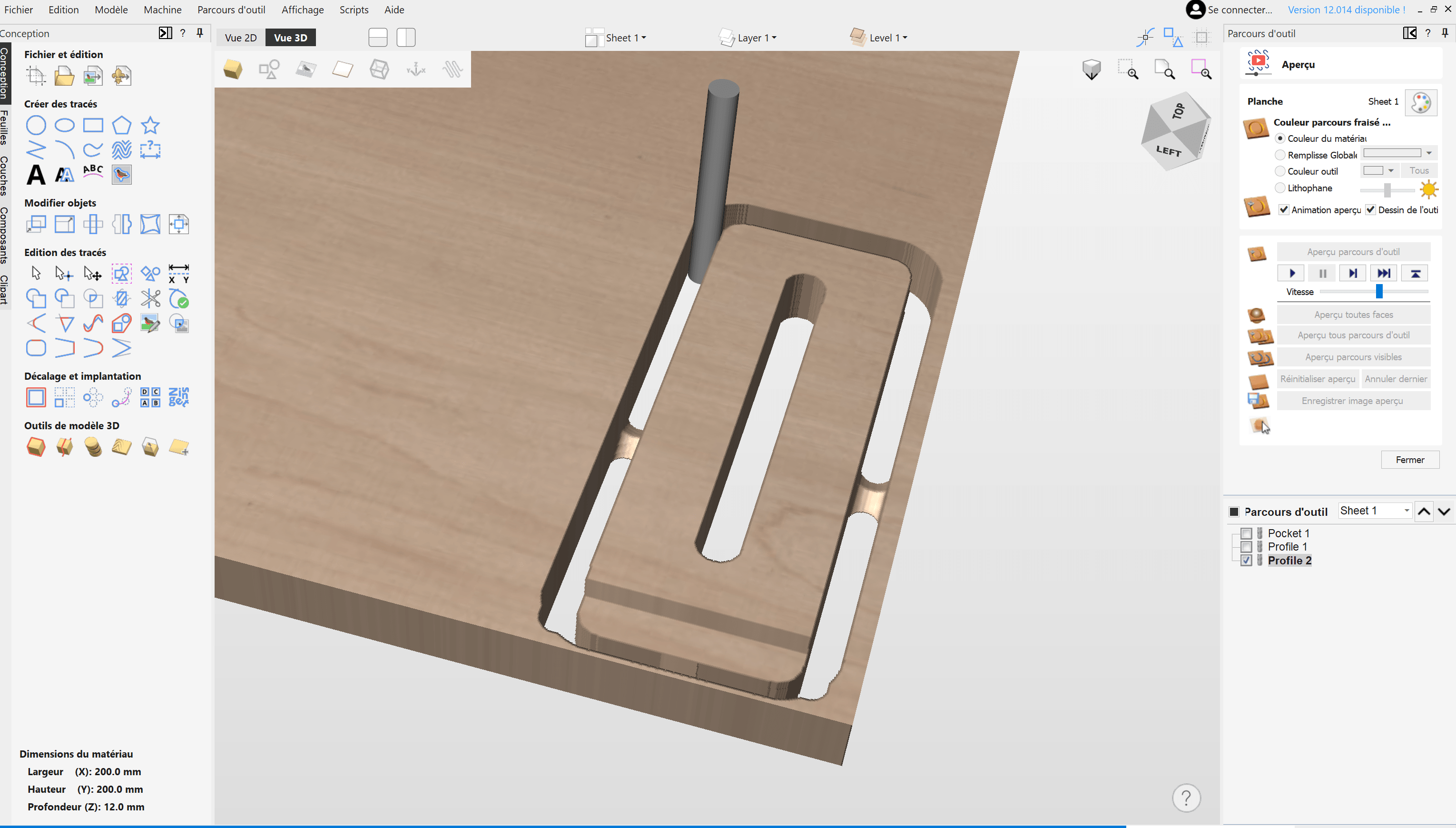
Learn how to create your project and generate G-Code from VCarve Pro or Aspire to easily machine your parts on a CNC milling machine.
Xavier K.
CNC Training
In this video, we show you how to turn your 3D file into proper G-Code using Fusion360 as a CAM (computer aided manufacturing) software.
If you want to dig further into the concepts seen in this video, read our detailed articles:
"Hi, it's Martin from Mekanika, In this video, I'm going to show you how to transform your 3D model into G-Code.
In the last video, we talked about 2D files and how to create a 3D model in the design section of Fusion360.
Now we're going to use the manufacturing mode to generate instructions.
Those instructions are called G-code. What we want to do at this step is to generate the toolpath of the different operations?
Let's see how to do that on the program."
"The first thing to do is to click on the drop-down menu over here on the left and select the manufacturing section.
You see that the top bar options change from 3D modelling options to different cutting operations.
Before creating any operation, we need to define our stock."
"The stock represents dimensions of the initial raw material you want to cut.
You need to choose a stock that is larger than the part you want to cut, since you will need space on the sides to clamp the part on your work table.
Here, we chose a square of 15cm and 12mm thick.
Now we have to define the orientation of that stock according to the XYZ axis of your machine.
Let's go back on the computer to create that setup.
Click on the setup icon. You see that two things appear: The first one is the transparent box with three axis system all around your model and the other one is the setup menu.
You first need to choose the orientation of these three axes. Click on the drop-down menu "WCS" and choose a way to define them. As you just saw, the Z-axis is always vertical. So click on the vertical edge of your model to define it.
Let's do the same with the X or Y-axis.
We now have to define the dimensions of our stock.
If you click on the "Stock" tab, you can access its options. As you can see, you have many ways to define the exact size of your stock. Let's choose "add stock to all sides". In our case this is 55mm in the X direction and 25mm in the Y direction.
You can verify the final dimensions of your stock just below.
Before closing that window, go back on the "WCS" tab and define the stock point. We recommend to always define that point on the left lower corner. Thanks to this, all your G-code instructions will be positive. You can then easily notice that there is a problem if you see a negative instruction. But you will understand it better soon.
You can now press enter and validate this setup.
Now that we have our stock defined, we have to choose the right tool to cut it.
We saw that our pocket is actually 8.5mm wide, so we can cut it with a 6mm 3-flutes flat end mill.
I know it sounds complicated, so if you want to know more about how to choose the correct end mill, go to our website. The link is in the description below
Back to Fusion360 to define that tool in our library. Click on the "Tool library" icon over here. The tool library window opens, and you see that there are already some Fusion360 tools encoded, But you can of course add your own tool. Select your local library and click on the "+" icon.
There exist many different types of end mills, but here, we're gonna choose the flat end mills type. In this sub menu, you can define all the characteristics of your end mill.
We will focus on three of them: The "General", the "Cutter" and the "Cutting data ».
The "General" tab allows you to give name to your tool or even to link it to your end mill suppliers.
On the "Cutter" tab, you need to define the type and the geometry of your tool. Simply measure your end mill and fill the blanks with the correct information. In our case, we'll use a 3-flutes, carbide, diameter 6mm, shaft 6mm as well, 50mm overall, 25 in the holder, 25 shoulders and 20mm flute length
The "Cutting data" section is maybe the most important part of it. This is where we define the Feeds and Speeds, which means that we tell Fusion how fast we want to cut the material. Here we cut plywood with a 6mm tool, So I know that on a Mekanika Pro Series, we can set 15,000rpm as spindle speed and 2,000mm/min as feed rate.
Lead-in, lead-out, plunge and ramp speeds are different types of approaches. No need to go further on that now, but you can set 1500 for lead-in, lead-out and ramp and 300 for plunge.
If you want to know more about Feeds and Speeds, go read the article on our website.
You can now click on the accept button, and see if the tool has been added correctly into the library."
"OK, now that we have added our tool and that our setup is ready, we can begin to define the milling operations.
Let's start with the simplest operation: cutting that hole.
To achieve this, we're going to stay in the "Manufacturing" section of Fusion360 and click on the 2D drop-down menu. You see that Fusion proposes different types of 2D operations. For the first step we are going to use the "Bore" operation.
A "Bore" operation is used to create cylindrical holes or islands. In Fusion, the 2D operations are always separated in 5 tabs:
"Tool" obviously concerns the tool you choose and the Feeds and Speeds related to the operation.
"Geometry" is the tab where you have to select the edges or faces to mill.
"Heights" allows you to set the different heights concerning the top or bottom.
"Passes" is for example, where you define the depth of cut.
And "Linking" is to tell the machine how to approach or move between the different operations.
Just so you know, simply remember that all the operations are split in the same five tabs.
Let's start with the tool. Browse the tool library and choose the end mill we've just created. Verify that the Feeds and Speeds are correct.
Go to "Geometry" and select the face of the hole you want to cut.
In the "Passes" tab, you have to define the pitch of the "Bore" operation. In our case, we will set 2mm. If you want to know more about all the other options, just leave your mouse on it for a second.
On the "Heights" and "Linking" tabs, nothing has to be changed
Click OK, and admire the toolpath of your first operation.
OK, next we want to cut the slot and the pocket. To do it, we need to use the 2D pocket operation. You recognize the five same tabs, so you know that we will start by defining our tool.
By default, Fusion shows the last tool you used. In our case this is what we want, So let's move to the "Geometry" tab.
For a pocket operation, you can either select faces or traces. In this case we are going to use the two possibilities. Click on the traces to select the slot and on the face to select the pocket. Once again nothing to change on the "Heights" tab.
On the "Passes" tab, you can remove the default stock to leave. You can activate the multiple depth option and set 3mm. You can also activate the both ways option. This means that the tool will cut in the two directions.
Finally, you can remove the lead in and lead out on the "Linking" tab.
Click "OK", and we're done with the pocket operation
Finally, let's cut the outline of our object. I’m sure you got it: we will need the "Contour" operation. Keep the same tool, and select the trace on the "Geometry" tab.
Activate the "Tabs" option: this will create contour tabs needed to keep the piece in place once the cut is finished. You can define their position either by typing it or clicking on the edges of the model.
Once you think it's okay go to the "Passes" tab to define the depth of the cut. Set 3mm as the depth of cut.
Remove lead in and lead out but keep the ramp. This will create a smoother cut.
Click "OK", and that's it!
All the operations are defined, but before going on the machine, we need to be sure that we didn't make any mistakes. For that, Fusion integrates a really cool feature: the machining simulation.
Click on your setup to select all the operations, and then click on the "Simulate" icon. You see that the "Controller" menu appears and allows you to play the milling sequence.
Verify the tool path, check if the stock is correctly set up and many other things."
"OK, now all our operations are defined and the simulation seems to be pretty perfect, But it's not G-Code yet.
To generate that G-code, we need a post processor. Click on the "Post Process" icon and choose the post processor which corresponds to your machine.
There are as many post processors as there are machines, But most of them will be installed by default with Fusion.
If you use a Mekanika CNC Machine, check out our article to know how to install the right post-processor. The link is in the description below.
At this step, you can give a name to your program or comment it if needed.
Click "OK" to export your G-code. Wait for a second.
A text editor window should pop up, showing you all the lines of your program.
OK, we're finally done with the computer work. Let's get our hands dirty on the machine."
Mekanika is a Belgian company based in Brussels whose ambition is to make local production more accessible thanks to a 100% open-source approach.
We design and produce high quality machines for CNC milling and screen printing, which have been recognized for their reliability and ease of use. Our tools are delivered as kits and fully documented, allowing to easily adapt them to specific needs.
Visit our shop to find out more, or check out our online resources and tutorials to continue learning.
Learn how to create your project and generate G-Code from VCarve Pro or Aspire to easily machine your parts on a CNC milling machine.
Xavier K.
CNC Training
Hot engraving, cold engraving, tools and tutorials: everything you need to know about wood engraving with your CNC machine.
Quentin L.
Content Creation
Learn how to create your project and generate G-Code from Carveco to easily machine your parts on a CNC milling machine.
Quentin L.
Content Creation