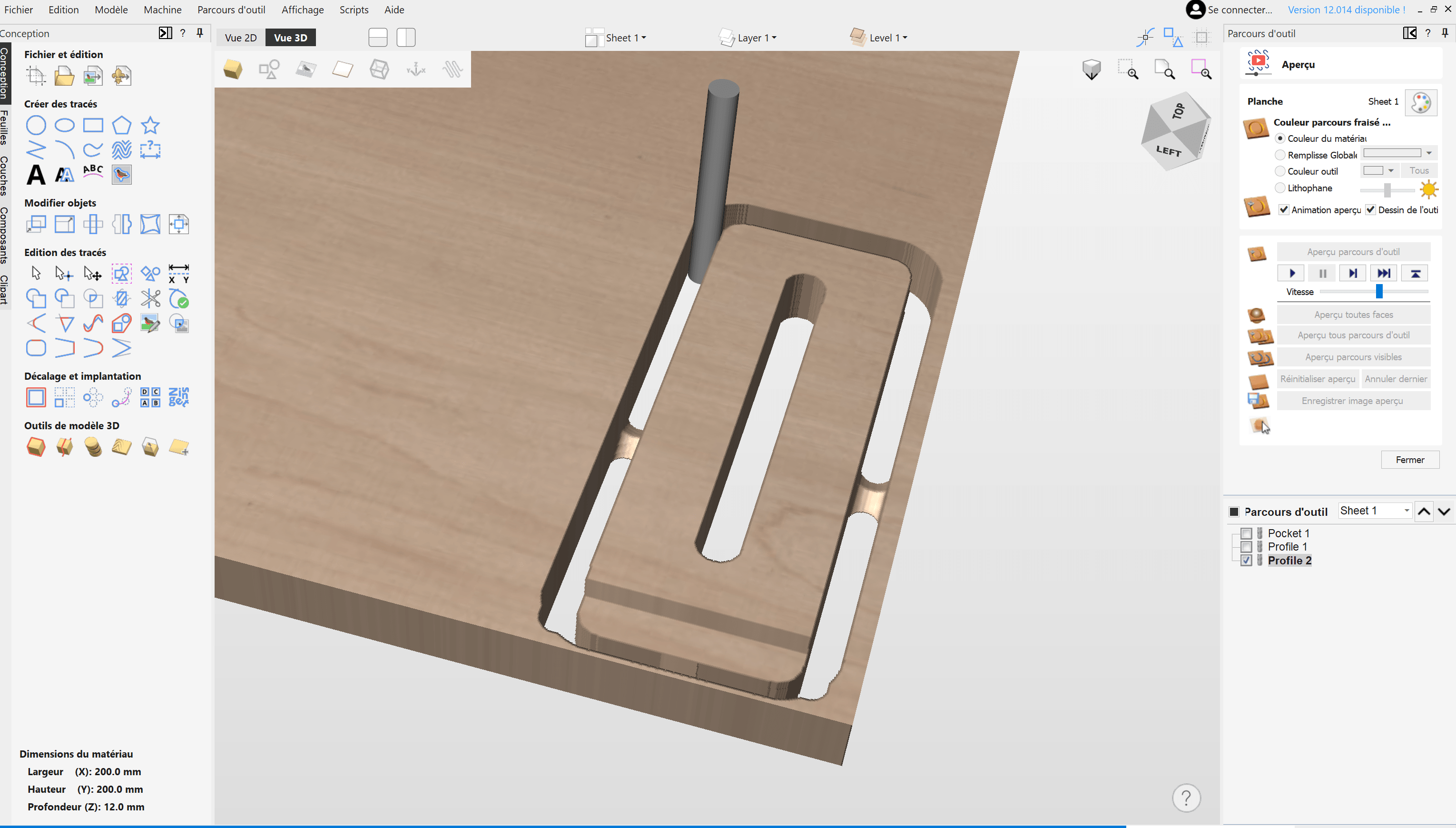
Learn how to create your project and generate G-Code from VCarve Pro or Aspire to easily machine your parts on a CNC milling machine.
Xavier K.
CNC Training
There are recurrent questions in the world of aluminium framed CNC machines :
Having the right spoiler board, according to the way you use your machine, can be a piece of life-changing equipment.
In this article, we will simply try to summarize what are the different possibilities and what are their respective advantages and drawbacks.
The easiest, cheapest and fastest solution consists in simply fixing a wooden board on the frame of your CNC machine. If you plan to work this way for a long time, your table board has to be considered as a consumable part because you will need to change it often.
- Advantages: Really Cheap, Easy to set up, large clamping resolution
- Inconvenients: Only wooden screws can be used to fix a piece, rapidly wasted, no Z reference
- Conclusion: Ideal for beginners
Having a nice flattened surface as a working area is the first step to use a CNC precisely. This is what you will work with once you got skilled with your CNC Machine. The good news is that you can easily transform your rough spoilerboard into a nice flattened one. Here are three possibilities to do it :
This technique consists in milling your current spoilerboard. In most of the cases you won’t be able to machine it on its full surface, so it will then create a gap at the lateral and back borders. This might be annoying to fix bigger pieces than your working area.
- Advantages: Easy to make, Z0 reference
- Inconvenients: Only wooden screws, rapidly wasted, problem if the piece to mill is bigger than the working area
- Conclusion: meaningless without a clamping system as this is going to be wasted very quickly
The second technique consists in adding another board fitting your working area. This board can be either glued or screwed to your rough board. By doing this, you will create a small step perfectly referenced with your router once surfaced. This is the most common solution, but it can be annoying if your Z clearance is not enough high.
- Advantages: Easy to make, Z0 reference
- Inconvenients: Only wooden screws, rapidly wasted, reduce the Z clearance
- Conclusion: meaningless without a clamping system as this is going to be wasted very quickly
The last solution consists in milling your current spoilerboard on its entire surface. This technique creates a perfectly leveled plan on the whole surface.
- Advantages: Easy to make, Z0 reference, fixing holes can be milled by the machine itself
- Inconvenients: Only wooden screws, rapidly wasted
- Conclusion: meaningless without a clamping system as this is going to be wasted super quick
*This example of a flattened surface will be the reference for the next type of spoiler boards.
However, a flattened spoilerboard is pretty much meaningless if the only way to fix pieces on it is to use wooden screws. This is the reason why the following examples deal with clamping systems. We will talk about three major clamping systems: threaded inserts, T-slots and vacuum table.
This fixing grid, coupled with adjustable clamping accessories is flexible enough to satisfy 90% of the jobs.
As the resolution of your grid is obviously related to the future clamping possibilities, we commonly see a 10x10 cm grid as a good start. But keep in mind that this grid system might need a lot of inserts according to the size of your CNC machine and the resolution you choose.
The real big advantages of this system are that the machine can mill precisely all the holes, which means that nothing more is needed except having a flattened surface and a bunch of threaded inserts.
- Advantages: Cheap, easy to set up/ large clamping resolution / can be milled by the CNC machine
- Inconvenient: Can be weak according to the type of wood and the thickness/ need adjustable clamping accessories
- Conclusion: Really good solution for Advanced & Pro
The second possible technique is the widely used : we're talking about wooden T-slots.
If you are a carpenter or if you have easy access to a wood workshop, this clamping system is really quick to set up. Once you have cut the wooden laths at the right size, you simply need to profile them with a manual router. Afterwards, you can either glue or screw them on your existing spoilerboard before flattening them.
You can also cut those profiled laths with your CNC machine.
- Advantages: Cheap, large clamping resolution, can be cut by the CNC machine itself
- Inconvenients: Can be weak according to the type of wood and the thickness used, reduce the Z clearance
- Conclusion: Really good solution for Advanced & Pro
In the series of T-slot tables, the second possibility is to insert some aluminium T-tracks into a wooden spoilerboard.
Once again, all the slots can be made by the CNC machine to be sure they are precise. Moreover, those aluminium T-tracks are in general more rigid than wooden T-slots (depending on the wood and the thickness), but they are also more expensive.
- Advantages: Rigid fixture, slots can be milled by the machine itself
- Inconvenients: Expensive, rapidly wasted
- Conclusion: Really good solution for Advanced & Pro but more expensive than the two previous ones
The last way to install T-slots on your CNC machine is to use wide T-slot aluminium profiles.
This solution will considerably increase the general rigidity of your machine and the rigidity of your fixing point. But keep in mind that those extruded aluminium profiles are never perfectly flat and in most cases, you won’t be able to flatten their entire surface. This causes the need to add a linear spoilerboard on top of them, which you can flatten. This technique is pretty convenient as your linear boards can be easily removed or changed and the aluminium slots assure strong fixing points. But if your Z clearance is low, it can be a bad choice.
- Advantages: One of the strongest and most rigid fixture, large fixing area
- Inconvenients: Expensive, can be complex to install, reduce the Z clearance
- Conclusion: Really good solution for Pros
Finally, we wanted to rapidly present you the vacuum solution.
This clamping solution appears as being the holy grail for any CNC user : thanks to the vacuum pump, any part can be fixed rapidly and securely, with no matter how big or thick the part is. These vacuum systems aren't really common on small CNC's, but they become almost necessary once working on big panels.
However, having this kind of system on your own CNC is pretty expensive because you will need a powerful vacuum pump and a hose system connected to your table. Which can cost up to several thousands euros.
If you are interested, you can check our guide on how to build a vacuum table, or check the model of vacuum table we propose for our machines.
- Advantages: The strongest and most rigid fixture/ the most flexible
- Inconvenients: Really Expensive due to external vacuum pomp, complex to install
- Conclusion: Best solution for the pros
To conclude, we can separate the spoiler boards into three different types.
The first one is the simple wooden boards in which you can fix any pieces with screws. This solution is good for beginners as it allows you to make mistakes without damaging your flat surface. But it has his limits in term of work precision and durability.
Once you get skilled, you will rapidly move to the flattened board types. Those spoiler boards have to be used with a clamping system such as threaded inserts grid or T-slots. Those two solutions appear as being the most common working surfaces in the world of aluminium-frame CNC. They are easy to set up, easy to clean or repair and (for most of them) affordable.
If you want to reach the next level you can still upgrade your machine by installing the vacuum pump system. Thanks to this clamping technique you can get rid off every bolt and screw while increasing the strength of your fixture.
Mekanika is a Belgian company based in Brussels whose ambition is to make local production more accessible thanks to a 100% open-source approach.
We design and produce high quality machines for CNC milling and screen printing, which have been recognized for their reliability and ease of use. Our tools are delivered as kits and fully documented, allowing to easily adapt them to specific needs.
Visit our shop to find out more, or check out our online resources and tutorials to continue learning.
Learn how to create your project and generate G-Code from VCarve Pro or Aspire to easily machine your parts on a CNC milling machine.
Xavier K.
CNC Training
Hot engraving, cold engraving, tools and tutorials: everything you need to know about wood engraving with your CNC machine.
Quentin L.
Content Creation
Learn how to create your project and generate G-Code from Carveco to easily machine your parts on a CNC milling machine.
Quentin L.
Content Creation