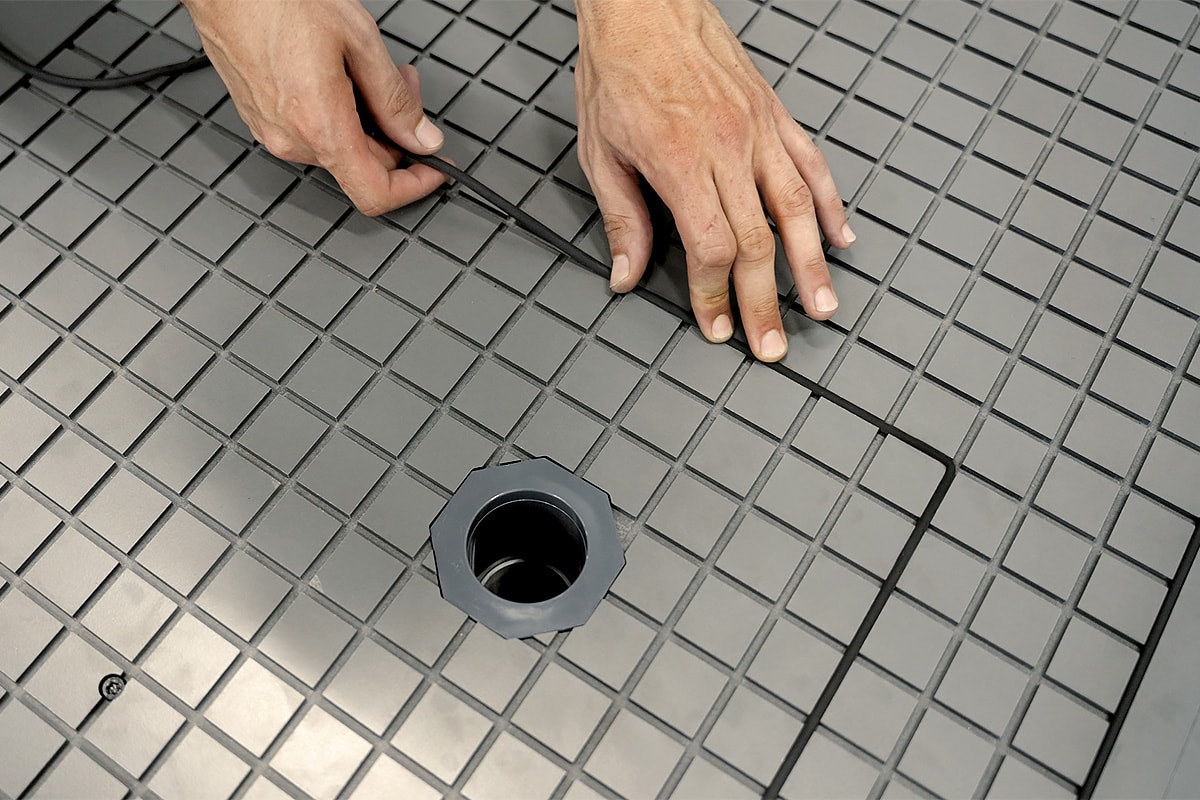
Find out how to maximize the performance of your vacuum table by learning practical tips on cutting strategies, spoilerboard maintenance and many more.
Maxime G.
Product Engineering
When it comes to working with panel-sized materials, such as plywood, MDF, or plastics, securing them before machining can be a challenging task, but also a time-consuming one.
This is where the ingenious solution of vacuum tables comes into play.
Vacuum tables have gained popularity as the go-to clamping solution for large CNC milling machines and for good reason. They offer a level of easiness and versatility that is hard to match with traditional clamping methods.
Whether you're a seasoned CNC professional or just stepping into the world of CNC machining, understanding the advantages of vacuum tables is essential to unlock the full potential of a CNC milling machine.
In this article, we will go through the construction of a simple vacuum system that can be installed on our CNC Fab model.
We will also explain key concepts that will help you understand the most important aspects of a vacuum system and guide you on how to adapt this design to your own setup.
Let’s start with a very brief explanation of vacuum physics, this will help us understand how to optimize our design.
Not interested in theory? Go directly to chapter 3 for the build.
The standard atmospheric pressure at sea level is 101325 Pa, or more or less 1 bar. This pressure is generated by the weight of the air around us, which can change depending on the altitude and weather conditions. To create a vacuum, it is therefore necessary to generate a pressure lower than the atmospheric pressure, within a specified volume.
Vacuum tables operate by using this pressure differential between the vacuum beneath a workpiece and atmospheric pressure above, generating a hold-down force.
This force is directly proportional to the pressure difference and the exposed surface area. Consequently, larger parts can experience substantial holding forces, while smaller parts are subject to lower hold-down forces.
Consider the example below:
In this case, we have a side-channel blower that can generate a pressure difference of 250 mbar under a 50cm by 50cm plywood board. Following the calculation that the force is proportional to the pressure difference and the usable vacuum surface, we see that the workpiece will undergo a
In this case, we have a side-channel blower that can generate a pressure difference of 250 mbar under a 50cm by 50cm plywood board. Following the calculation that the force is proportional to the pressure difference and the usable vacuum surface, we see that the workpiece will undergo a hold-down force of 625kg.
In order to know if this force will prevent the workpiece from moving during a job, we need to make sure that the cutting forces stay below the holding forces acting on that board. There are 4 forces at play here:
In order to know if this force will prevent the workpiece from moving during a job, we need to make sure that the cutting forces stay below the holding forces acting on that board.
There are 4 forces at play here:
Fh is the hold-down force created by the vacuum + the weight of the board. From the theory of static friction, we know that this force creates a friction force Ff that prevents the board from sliding when the radial cutting force Fr is acting on it.
If an upcut end mill is being used, the axial cutting force Fa also has to be considered (although it is often much lower than the radial one, depending on the helix angle of the flutes).
If the vacuum table and the board are both made out of wood, the static friction coefficient has a value of 0,40. Neglecting the weight of the board, we find a total friction force of:
Ff = µ x Fh = 0,40 x 6250 = 2500 N
To give you a (very) rough comparison, a 6mm end mill cutting through plywood with a 100% tool engagement, 6mm cutting depth and at 5000mm/min would generate a radial cutting force in the range of 50 N. As you can see, there’s no risk of seeing the workpiece move during the cut.
Keep in mind that the hold-down force calculated in this example is still a theoretical value. In practice, there are a few factors that can reduce the force, such as:
Regarding the last point, you should always consider that the effective surface upon which the vacuum force is acting applies only to the area with channels or grooves.
Therefore, it is the surface area of the covered channels and not the surface area of the actual workpiece that will determine the hold-down force. This consideration will influence the design of our table, as you will see later.
Ok, enough of theory, let’s talk practical and discover how to implement this on our CNC milling machine. In short, a vacuum system is made of the following main elements:
Let’s dive into the specifications of each part of this system and understand how they work together.
Many kinds of machines can be used to create a vacuum, but we are mainly interested in two types here:
Here is a simplified table that highlights the differences between each type. The reality is of course more nuanced, as there are many different models at many different price ranges for both, but this should give a hint on what you should go for when designing your vacuum table.
|
Side channel blower |
Vacuum pump |
Airflow capacity |
High |
Low |
Vacuum level |
Low |
High |
Cost |
Affordable |
Expensive |
Durability |
Prone to failure |
More robust |
Thanks to their high airflow capacity and affordability, side channel blowers are often the preferred solution for large CNC milling machines, as the size of the workpieces compensate for the lower vacuum levels (remember the formula: if the pressure difference goes down, the same hold-down force can be applied if the surface of the workpiece increases).
One thing to keep in mind though: they can be prone to failure, usually caused by particles or chips entering the chamber and jamming the impeller. Likewise, if there is insufficient airflow, the impeller will overheat and expand, leading to a potential fusion with the housing and catastrophic failure.
As a result, it is highly recommended to install a proper filter on the inlet, as well as a pressure relief valve that will allow a minimal airflow to circulate at all times.
In contrast, vacuum pumps are well-suited for smaller CNC milling machines, with workpieces that provide a smaller vacuum area. They rarely experience failure and represent a cost-effective solution that will require low maintenance.
The plenum is a grooved board with one or several holes leading to the vacuum pump. When the pump is turned on, a vacuum is created inside these free channels and any material put above them will be sucked down. To avoid leaks and loose vacuum performance, a soft rubber seal is often placed inside the grooves at the perimeter of the workpiece.
You can see in this design that the effective vacuum area has been optimised without compromising the rigidity of the whole board, using a cross-pattern on each holding square. This will lead to a significant increase in the hold-down force.
To channel the airflow toward our pump, there are a few possibilities. The first one consists of employing flexible hoses and pneumatic connectors. This proves to be an efficient method, facilitating a speedy and straightforward installation process.
While this approach is ideal for smaller vacuum tables, caution is advised for larger vacuum systems, as the small hose diameters will limit the airflow.
For larger vacuum tables, it is recommended to use PVC pipes and their standard connectors. This provides a cheap and easy solution, with parts that can be found in any hardware store.
Moreover, when designing a larger table, the creation of several zones should also be considered. That can be achieved using sealed end caps for each zone, or by having valves that will allow to easily open or close each one before a job.
The complete vacuum setup often ends with an MDF spoilerboard (also called bleeder board), which comes on top of the plenum. The benefit of this approach is twofold.
First, it will protect the expensive part of the vacuum table from any machining mistakes, as it is more painless to replace an MDF board than a machined plenum. At the same time, it will prevent dust and chips from entering the vacuum pump.
Secondly, as MDF is a porous material, the board will distribute the vacuum from the channels evenly across the entire surface. That way, the effective area on which the vacuum pressure is applied is greater, generating a stronger hold-down force.
While this method proves effective, it’s important to understand that it requires a side channel blower capable of extracting a greater volume of air, since the bleeder board will leak air from any area that isn’t covered by the workpiece.
To illustrate this point, consider the performance curve of a 1.5kW side channel blower, which plots the pressure differential achieved versus the airflow rate.
You can immediately see that the vacuum is inversely proportional to the airflow. Let’s say that our MDF board leaks 90 m³/h, then the available pressure difference is only 150 mbar, compared to 285 mbar with a perfectly sealed vacuum, generating almost twice less force!
Of course, it is also possible to combine both techniques. You can create a vacuum jig by placing a sealing cord under the spoilerboard at the exact dimensions of your workpiece, to contain the vacuum area and remove a large portion of leaks.
The build from this how-to article is intended to provide a cheap but performant vacuum table for a panel-size machine. Due to budget considerations though, some ergonomic improvements that were mentioned above were left out, feel free to add them to your own setup nonetheless.
We decided to work with two 2.2kW side channel blowers that will be connected in parallel, allowing us to have more airflow capacity and maintain a good vacuum.
This also provides a cheaper option than purchasing a larger and more powerful blower and allows us to stay within the range of monophase motors (larger side channel blowers will most of the time require that have a triphase outlet). If your budget allows it though, consider getting a vacuum unit from Black Box Vacuum, as they offer a great price/quality ratio.
The plenum will be made using the standard MDF boards from our catalogue as a basis, as it is cheap, and modular (only one part can be swapped if damaged). But of course, you can also use an entire panel to make the table, you will just have to adapt the g-code provided (link to fusion project below).
If you want to go for a more premium version, we recommend using plastic boards made of PLA or nylon, as they are easy to machine and will provide a very stable plenum.
Most of the time, starting with a face milling operation is desirable, since it levels your work area perfectly. We decided to avoid it and keep things simple here, as the top layer of MDF isn’t as porous as its inside.
This prevents us from surfacing everything and having to apply a composite product on the whole top surface of our plenum to make it airtight (this doesn’t apply if you use another material than MDF of course). The perfect levelling will be achieved later with the use of a faced mill bleeder board.
If you want to face mill nonetheless, then use wood sealer on the machined surface and apply some on the sides of the board also, to minimize leaks even further. In this case, we also recommend using thicker boards, to keep enough rigidity even after removing some material (25mm boards instead of 18mm would be a good option for instance).
As just explained, we will use a thin MDF bleeder board above the plenum, that can be used as a spoilerboard and will prevent the table from being damaged if the tool goes too low during a job.
We will also use a sealing cord on the plenum to define precisely the zones where the vacuum has to be applied and get a good sealing effect. This allows you to use less performant side channel blowers and still obtain good results.
At last, we will use gate valves to open/close 4 defined zones on the plenum. Again, this allows us to optimise the effective vacuum area when we are not milling an entire sheet.
This section provides a step-by-step guide on how to manufacture the plenum of our vacuum system and how to implement a complete piping network with 4 zones.
Here are important links that you will need for this build:
Let's go!
Verify that your machine table frame is very well levelled. You need to have a good flat working area to start well, especially since we won’t face mill the boards.
Attach the four spoilerboard parts. Make sure that they are well-aligned and that each screw is well-tightened.
Turn on your machine and wait for PlanetCNC to load.
Home the machine and square the gantry.
Without changing the machine position, enter the following working coordinates: (X73.5 ; Y66)
Insert an 8mm flat end mill (3-flute in our case), and leave 40mm of stick-out to allow the machine to mill all the way below the plenum, otherwise, the machine will throw a machine limit error.
Use the Z-axis probe to measure the tool length and zero the axis on the top surface of the plenum.
Put the dust shoe on.
Load the G-code and start the program.
When the 4 holes are milled, the machine will stop for a tool change. Change the current tool for a 5mm flat end mill (2-flute in our case).
Don’t forget to make a new tool measurement to recalibrate the Z0.
Press the pause button to continue the program.
When the program is finished, move the gantry at the back. Gently sand the edges of the cut with fine sandpaper and vacuum clean the whole plenum.
Start by opening the 3D assembly of the whole system to understand how everything will be connected.
The piping system consists of a network of 63mm PVC pipes normally used for water discharge. You can use PN10 or PN16 pressure pipes if you want, but it will add an unnecessary cost to your assembly.
The zones will be activated with the use of 63mm gate valves, which will all be interconnected through a 90mm manifold. This manifold consists of four 90mm tees assembled and housing a 90-63mm reduction at the top.
First, you will need to cut the 63mm PVC pipes to the necessary dimensions:
Once done, use a belt grinder to create a slight chamfer on each side of the pipes that have been cut. Then, sand the surfaces that have to be brought into contact during the assembly, both on the male pipe and the female connector.
When done, blow the pipes entirely to remove the dust from all the faces, but also from the inside (you don’t want that dust to end up in your vacuum system later on).
Now, you will need a caulking gun with all-purpose glue to attach the four 140 mm PVC pipes on the plenum, creating the outlet for each zone.
Put glue on both the PVC pipe and on the plenum hole inner surface. Then, insert each PVC pipe into each hole, making it flush with the grooves of the plenum. Leave to dry for several hours, as indicated on the glue instructions. This will create a strong bond that is at the same time airtight.
While the glue is drying, start assembling the piping network. Before applying any PVC glue, try to assemble everything dry to make sure everything fits and is at the right length. You can also use a marker to mark the nesting depth of the male tubes inside the female elbow connectors but also to make sure that you have 90° angles everywhere.
When ready, use a small brush to apply the PVC glue on each pipe and connector, one by one. Assemble first the intermediary parts, before glueing them to the plenum outlet, it will make things easier.
Pre-assemble the manifold as well, as it will be easier to fix it to the machine frame.
Lastly, connect the outlets of each zone with the pre-assembled pipes and valves. You might have to support the two longest pipes with clamps attached to the machine frame, as shown hereunder.
To secure the manifold to the machine frame, you will also need to use 90mm pipe clamps. Then, you can glue together the last parts, manifold and valve of each zone.
The procedure for this step will highly depend on the type of pump or side channel blower you have your hands on. Is it only one unit connected directly to the manifold or several to run in parallel (or series), what is the inlet diameter, do you need threaded connections... Therefore, we will not go into the details of that part of the build.
In our case, we decided to use two double-stage side channel blowers, single phase and 1.5 kW. We connected both in parallel to maximize the available airflow.
To create a cheap and ergonomic bleeder board, we decided to use a standard 6mm MDF board and cut it into 4 equal parts, one for each zone.
To face mill each board, we'll use the vacuum table for the first time! We want to remove 1,5 mm on each side to be left with 3 mm sheets.
Insert neoprene cord in the plenum grooves to create a sealing joint at the perimeter of each MDF board, on each zone.
Then, place the 4 boards on each zone and turn on the vacuum pump. You can now start the face milling operation (don't forget to use a dust shoe!).
When done, flip over the boards and repeat the same operation on the other side. After some quick vacuum cleaning, here's the result:
Going back to our example of a 50 x 50 cm plywood board with a pressure difference of 250 mbar (achieved on our side channel blowers when using sealing cords). Taking into account a 50% effective vacuum surface here, the board will undergo a hold-down force of around 300 kg.
Since it is placed on another wooden surface, the static friction force that prevents that board from moving is more or less 120 kg.
We used a simple dynamometer to verify that it wouldn’t move. We didn’t have enough strength to pull 120 kg, but managed to measure a force of 50 kg and indeed, the board didn’t move at all.
Satisfied with this result, we decided to put a smaller pine wood board on the vacuum table (this time, using the bleeder board on top of the sealing cord) and to use a 25 mm face milling tool. The operation went very smoothly, with very little vibration of the board since it was very well clamped, despite its small size.
That's it, you made it to the end of this long article!
Hopefully, you found it useful and could get some inspiration to create your own vacuum setup. Don’t hesitate to share your experience with us, or simply to reach out if you have any comments or remarks.
Mekanika is a Belgian company based in Brussels whose ambition is to make local production more accessible thanks to a 100% open-source approach.
We design and produce high quality machines for CNC milling and screen printing, which have been recognized for their reliability and ease of use. Our tools are delivered as kits and fully documented, allowing to easily adapt them to specific needs.
Visit our shop to find out more, or check out our online resources and tutorials to continue learning.
Find out how to maximize the performance of your vacuum table by learning practical tips on cutting strategies, spoilerboard maintenance and many more.
Maxime G.
Product Engineering
Learn how to create your project and generate G-Code from VCarve Pro or Aspire to easily machine your parts on a CNC milling machine.
Xavier K.
CNC Training
Hot engraving, cold engraving, tools and tutorials: everything you need to know about wood engraving with your CNC machine.
Quentin L.
Content Creation