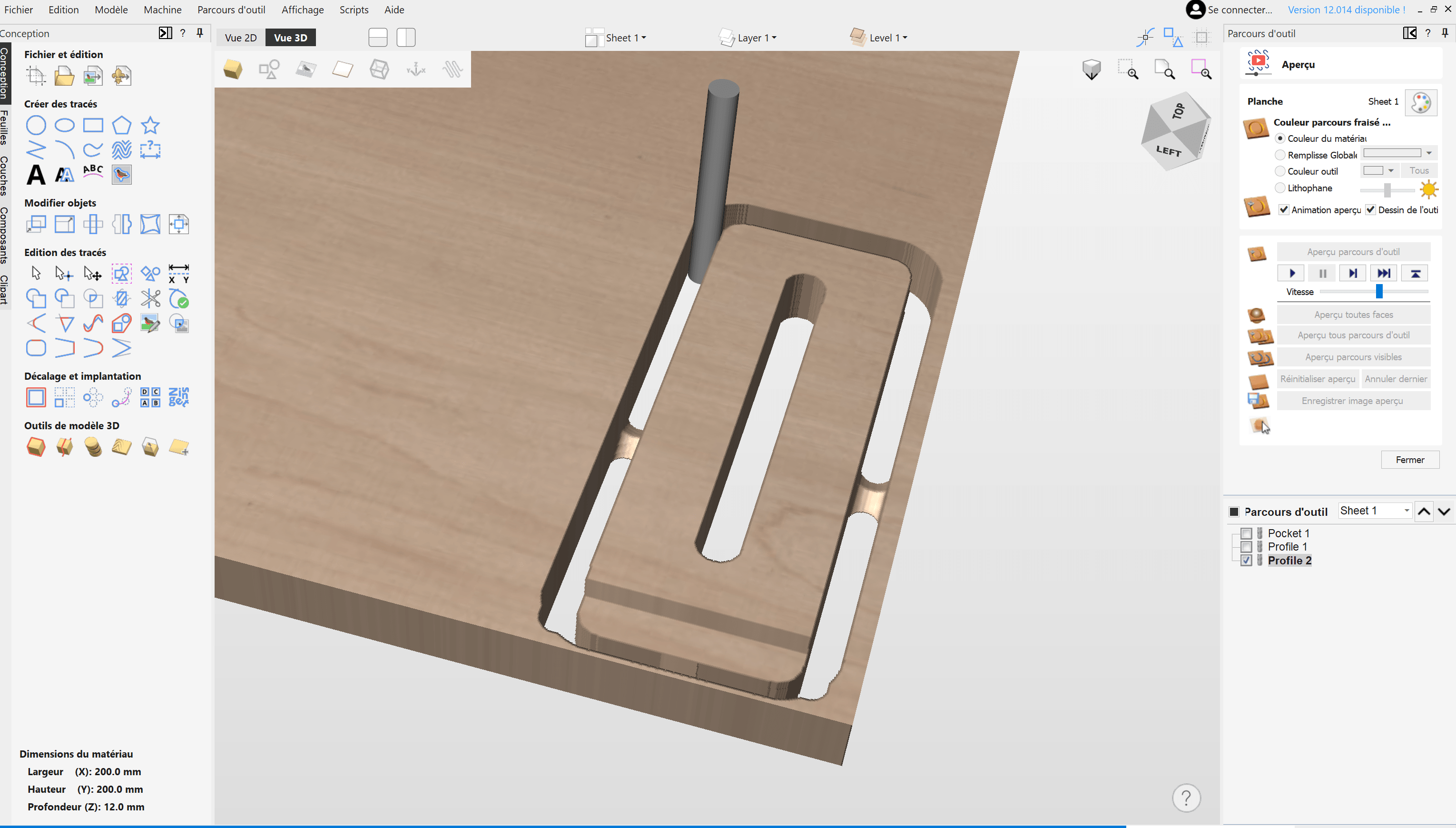
Learn how to create your project and generate G-Code from VCarve Pro or Aspire to easily machine your parts on a CNC milling machine.
Xavier K.
CNC Training
One of the most common questions we get from makers interested in CNC milling is the following : which CNC software should I use? Before diving into software recommendations, this guide will walk you through the following sections.
Let's start by understanding the different types of softwares at play.
There are 3 different types of software that are used in the process of milling:
While there are three categories of software, a single tool (e.g. Autodesk Fusion 360) can sometimes offer a combination of a couple of them, which makes them even more complex to understand.
Simply put, CAD is the software you're going to use to design your parts. You're going to go from sketches (drawings in 2D) to objects in 3D.
If you're comfortable with 2D drawing software like Illustrator or Inkscape, you can start from there, and import *.dxf files into your CAD software.
If you're not, you can directly learn to do 2D sketches on the CAD software you're going to pick.
This is the software that allows you to generate machine instructions (G-code) to manufacture your object. It always goes like this:
Often, CAD and CAM software goes together as one solution. But you can also decide to separate the two, for example, if you're already familiar with a CAD software that doesn't have CAM capabilities.
Let's have a look at the last type of software, then discuss the existing solutions out there.
This last type of software is simply the interface you're going to have to control your machine. Most desktop CNC machines don't come with an onboarded computer, so it's a software you may install on your laptop to connect it to your machine.
When it comes to machine control software for CNC desktop machines, some of the big names include Mach3, LinuxCNC and GRBL/USG. Before diving deeper into the pros and cons of each software, we need to understand how a CNC milling machine is controlled. The electronics that control a CNC are basically composed like this:
The criteria to decide the best software for your usage should be:
For versatile usage in wood, metal, foams or plastics, here are the most used software:
+ Advantages of Autodesk Fusion |
- Downsides of Autodesk Fusion |
|
|
For more information on how best to generate G-Code from Autodesk Fusion 360, see our full video tutorial playlist on youtube.
+ Advantages of FreeCAD |
- Downsides of FreeCAD |
|
|
For more information on how best to generate G-Code from FreeCAD and use it on your CNC machine, see our dedicated tutorial.
+ Advantages of VCarve |
- Downsides of VCarve |
|
|
For more information on how best to generate G-Code from VCarve and use it on your CNC machine, see our dedicated tutorial.
+ Advantages of SketchUp |
- Downsides of SketchUp |
|
|
To find out how to generate your own G-Code from SketchUp, follow our comprehensive tutorial on the subject.
+ Advantages of SolidWorks |
-Downside of SolidWorks |
|
|
+ Advantages of CorelDRAW + CamDRAW |
- Downsides of CorelDRAW + CamDRAW |
|
|
For more information on how best to generate G-Code from CorelDRAW and use it on your CNC machine, see our dedicated tutorial.
+ Advantages of Carveco |
- Downsides of Carveco |
|
|
For more information on how best to generate G-Code from Carveco and use it on your CNC machine, see our dedicated tutorial.
Once you've mastered CAD and CAM software to design your parts and prepare your G-code for milling, you need to familiarize yourself with a CNC control software for your machine.
There are a lot of different software out there. Some are free or open-source, while others are linked to a specific control board or to a specific machine brand. It may be hard to make a choice, so here is our comparison of the most used CNC control softwares and why we've decided to implement PlanetCNC on Mekanika's CNC milling machine.
When choosing a CNC control software, pay attention to the following:
Let’s start with software that is not linked to a specific brand of machine.
Let's start with a software we consider to be one of the best options on the market s far: PlanetCNC.
PlanetCNC, a European brand comes with its own hardware. They have developed a single-board USB controller that allows up to four axes. They offer many nice features out-of-the-box, like automatic tool length measure or tool change, jump to line, override feed rate, and support all compensation methods for common milling operations, as well as 3D milling.
The software runs on Windows, Linux or Mac and is compatible to almost all CAM programs on the market and can import a vast variety of files like Gerber, PLT/HPGL, DXF or NC files.
When we started designing the Mekanika CNC machine, we tested several controllers and software and PlanetCNC came on top in terms of software stability and robustness of electronic components.
Plus, it runs perfectly on a Raspberry Pi 4, which allowed us to create a standalone electronic enclosure without any need to use an external computer.
+ Advantages of PlanetCNC |
- Downsides of PlanetCNC |
|
|
Mach3 is without any doubt the most used software on the desktop CNC market so far.
Mach3 is a control software compatible with many hardware solutions and has positioned itself as the market leader for desktop CNC control software. Its success is mainly historical, as it came in at a time when its interface was a lot more user-friendly than what existed on the market so far.
+ Advantages of Mach3 |
- Downsides of Mach3 |
|
|
The "father" of all low-end CNC software, created in 1993, is a free open-source Linux software. Most further control software have based their original code on the LinuxCNC project.
The project benefits from a huge open-source community that has developed several versions of the software and has contributed to the fact that it's still the second most used CNC control software today.
+ Advantages of LinuxCNC |
- Downsides of LinuxCNC |
|
|
Technically speaking, GRBL is a firmware which enables motion control for CNC machines, but it doesn't come with a user interface. It is actually an open-source software that allows microcontrollers like Arduino to receive G-code from a computer, through USB transfer.
It is usually combined with a G-code sender software that allows the user to transfer G-code to the Arduino. One open-source software has been sailing through the multitude of available software : the Universal G-code Sender, however most of the proprietary software from companies Inventables or Shapeoko are running on GRBL as well.
Recently, two new branches of the GRBL code emerged: grblHAL and fluidCNC, both taking advantage of the far more superior computing power of 32-bit microcontrollers (instead of the 8-bit Arduino). These are both promising projects that we are closely watching!
+ Advantages of GRBL + USG |
- Downsides of GRBL + USG |
|
|
Let’s continue with control software developed by CNC machine companies.
They all developed their solution on top of 8-bit GRBL.
Easel is the software developed by its mother company: Inventables, which developed the X-carve CNC machines. It comes as a free version or as a Pro version for 24$ / month.
The main purpose of Easel is to simplify the life of its user by integrating CAD/CAM and control into a single software that generates more or less all the machine operations. It also simplifies the machine setup process, automatically doing all the positioning procedures of the machine when you launch a job.
+ Advantages of Easel CNC Software |
- Downsides of Easel CNC Software |
|
|
Carbide – the parent company of Shapeoko CNC’s - has developed a similar approach as Easel, but in the more traditional form of two software: Carbide Create to design, and Carbide Motion to control the machine.
Carbide Motion has a very sober interface that cuts all the unnecessary options on a CNC machine to help you focus on the main features.
+ Advantages of Carbide Motion |
- Downsides of Carbide Motion |
|
|
Onefinity is built on top of Buildbotics, an open-source controller that runs its own control software. Like the two previous software, Onefinity is a very sober interface that cuts all the unnecessary options on a CNC machine to help you focus on the main features.
+ Advantages of Onefinity CNC software |
- Downsides of Onefinity CNC software |
|
|
In 2023, Onefinity launched their Elite models together with Masso, finally offering a proper interface for their users.
Masso is well known for their CNC controller and Onefinity has embedded its G3 model, a combined controller with a touch screen on their machine.
+ Advantages of Onefinity Elite |
- Downsides of Onefinity Elite |
|
|
Mekanika is a Belgian company based in Brussels whose ambition is to make local production more accessible thanks to a 100% open-source approach.
We design and produce high quality machines for CNC milling and screen printing, which have been recognized for their reliability and ease of use. Our tools are delivered as kits and fully documented, allowing to easily adapt them to specific needs.
Visit our shop to find out more, or check out our online resources and tutorials to continue learning.
Learn how to create your project and generate G-Code from VCarve Pro or Aspire to easily machine your parts on a CNC milling machine.
Xavier K.
CNC Training
Hot engraving, cold engraving, tools and tutorials: everything you need to know about wood engraving with your CNC machine.
Quentin L.
Content Creation
Learn how to create your project and generate G-Code from Carveco to easily machine your parts on a CNC milling machine.
Quentin L.
Content Creation