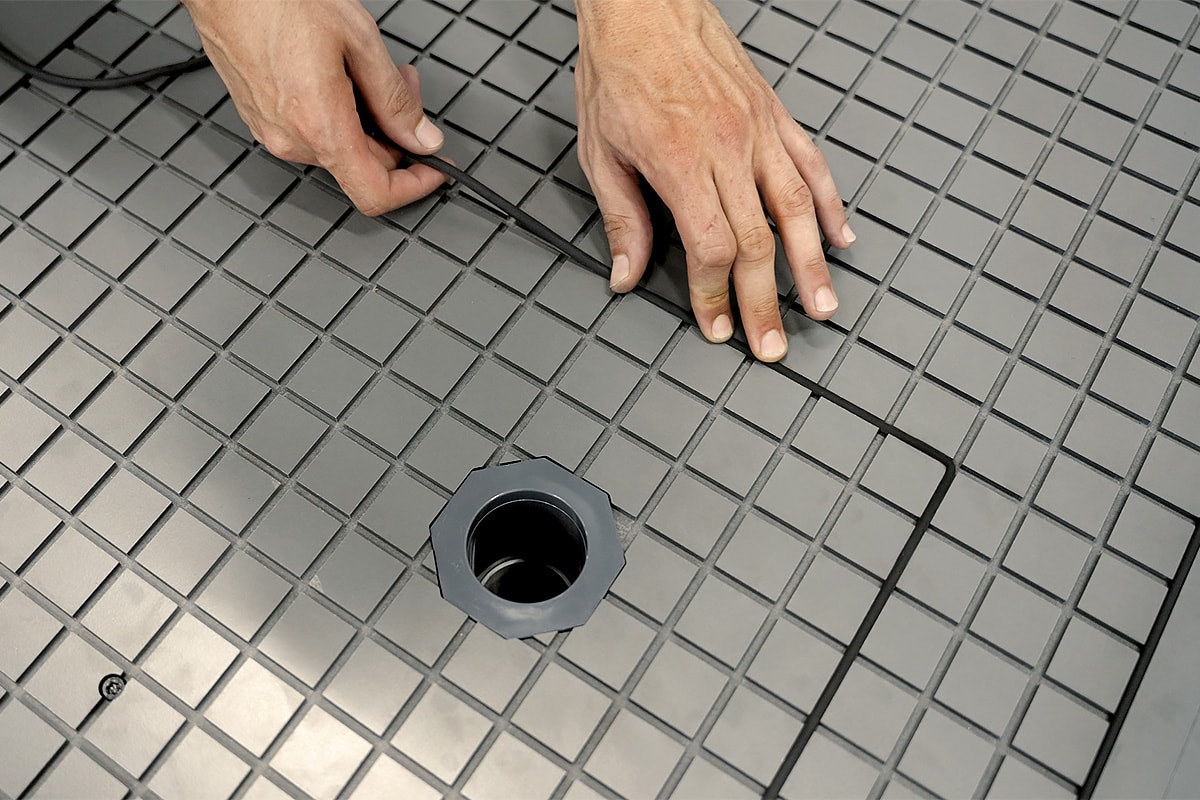
Find out how to maximize the performance of your vacuum table by learning practical tips on cutting strategies, spoilerboard maintenance and many more.
Maxime G.
Product Engineering
Carveco is an accessible CAM software that is easy to learn and will get you milling your first pieces very quickly.
In this tutorial, we're going to go through the toolpath creation process in Carveco Maker (the most basic version of Carveco) in order to mill our usual tutorial clamp as an example. By the end of this article, you should be familiar with Carveco's CAM interface and basic functions, and how to use it with your Mekanika CNC machine.
We will focus on the Toolpath window as in the context of this tutorial, we'll import our clamp *.DXF file directly, without drawing it from scratch.
If you wish to learn the basic concepts of CNC milling, we'd suggest you go through our tutorial series first before following this specific tutorial for Carveco.
Let's start by creating our new project.
Click on New Model and enter the dimensions of your stock in which we will cut our clamp, in our case it is 150 x 150 mm.
We can now import the drawing of the clamp.
Click on the menu Vector > Import, and select the .dxf file of the clamp (link above).
A window opens showing you the details of the .dxf file.
Don't change anything here and keep "auto. rejoin vectors" checked.
Then click OK.
The drawing is now imported and Carveco centers it automatically in your file.
One last step: In order to be able to mill the slot at the tip of the clamp, we will draw a rectangle defining the area to be milled halfway through to create that slot (as Carveco does not understand the milling of open paths).
We now need to place this rectangle above the slot.
Your drawing is now ready for the CAM preparation and should look like that:
Open the toolpaths menu of the project, on the right side of the screen.
The toolpaths menu appears underneath.
We can see in this menu all the tools around CAM:
Let's start setting up our material (stock) specifications.
Click on "Setup Material" and enter the material thickness (for us 12mm) and set the model position in material to bottom (this means our Z0 will be set on the spoiler board, to be sure the cut goes all the way through).
The software automatically sets the top and bottom offset.
Now we can start creating the operations. First we will cut the slot at the tip of the clamp.
We will now need to select a tool for the job.
The native parameters of Carveco for this tool correspond to our needs in this case, but just to check the menu, click on Edit and you'll see how you can edit the specifications, feeds and speeds of the tool here.
You can create and save copies of tools with different parameters in this library if you plan to reuse the parameters often.
You can now switch to the 3D view (top left of the view) and see the toolpath displayed. You can also use the simulation menu on the right to have a preview of the toolpath result.
Let's program the rest of the operations. The next operation is also a pocket toolpath for the hole and the groove:
We can see we now have 2 toolpaths in the list of the project on the right.
The last toolpath is the outline of the clamp:
In order to avoid the clamp moving when the cut is over, this will add some tabs to hold it to the remaining stock. You can set their size, the default 5x2mm is good for a plywood clamp.
If you are not very experienced, adding 4 tabs is recommended for secure holding of the finished part.
You can see their position may not be very logical - we want one tab in the center of each side.
All the toolpath are now done !
Your file is ready to be exported and sent to your machine.
A good practice is to simulate your full job before exporting anything to your machine, to see if it all seems like what you expect.
You can use the Simulate function of Carveco for that.
When you have checked the simulation and everything seems right, we're now ready to export our G-Code file.
This is the post-processor adapted to Mekanika CNC machines. If you use another machine, check with the manufacturer which post processor should be used.
We have another tutorial on how to use your Mekanika machine for the first time when you generate your G-Code, that you can find here and that is adapted to any software.
Congrats! You are now able to cut your own parts using Carveco!
Mekanika is a Belgian company based in Brussels whose ambition is to make local production more accessible thanks to a 100% open-source approach.
We design and produce high quality machines for CNC milling and screen printing, which have been recognized for their reliability and ease of use. Our tools are delivered as kits and fully documented, allowing to easily adapt them to specific needs.
Visit our shop to find out more, or check out our online resources and tutorials to continue learning.
Find out how to maximize the performance of your vacuum table by learning practical tips on cutting strategies, spoilerboard maintenance and many more.
Maxime G.
Product Engineering
Learn how to create your project and generate G-Code from VCarve Pro or Aspire to easily machine your parts on a CNC milling machine.
Xavier K.
CNC Training
Hot engraving, cold engraving, tools and tutorials: everything you need to know about wood engraving with your CNC machine.
Quentin L.
Content Creation